Productivity and innovation spotlight on automation at IMARC 2025
METS heavyweights Sandvik, Epiroc and Hexagon are in the vanguard of the technological shift that will be the most impactful in terms of productivity and safety in the global mining industry in the next decade.
The major trend is auto-mobility – and the speed of mining’s transition is now increasing significantly after a protracted period of regulatory and social-contract ground-breaking in the industry over the past 15 years or so.
What proof is there of a pronounced gearshift in level-three mobile fleet autonomy uptake, even as some miners and mining equipment, technology and services (METS) companies move further down the road towards level four and five technology?
The evidence is everywhere.
Canadian oil sands major Suncor says it has moved to 100% autonomous ore haulage at its giant Oil Sands Base operation near Fort McMurray in Alberta after the world’s biggest auto-ultra-class truck deployment (91 vehicles). This year it is targeting 100% autonomous waste tonnage movement with at least US$175 million a year of cost savings.
“Autonomous haulage is a key lever for Suncor to deliver a safer, more reliable and more cost-effective operation,” the $50 billion company says.
In neighbouring Saskatchewan, fertiliser minerals major Nutrien says it mined 35% of its potash ore tonnes using automation in 2024, “providing efficiency, flexibility and safety benefits, while supporting our highest annual production levels on record and a reduction in controllable cash cost of product manufactured per tonne”.
In Arizona, USA, copper heavyweight Freeport-McMoRan expects its Bagdad operation to become the first US mine with a fully autonomous haulage system this year. It is spending about $80 million to automate 33 large trucks and anticipates a range of benefits ranging from reduced hiring and housing pressures to diesel “emissions reduction expected from reduced idle time and improved efficiency”.
“The project will position us to capitalise on future technological advancements in electrification,” Freeport says.
At the new $2.16 billion Hermosa zinc-lead-silver project in Arizona, operator South32 has ordered about $80 million of Sandvik underground machines including trucks and loaders that will come automation-ready. South32 says it is designing Hermosa to be its first “next generation mine”, harnessing automation and other technology to drive efficiencies, minimise environmental impact and ultimately to target a carbon-neutral operation in line with its goal of achieving net zero operational carbon emissions. “Technology and innovation play an essential role in helping to improve safety and performance, and reduce our emissions,” South32 Hermosa president Pat Risner said.
And in Western Australia, where Epiroc has been working with Hancock Iron Ore on a major mix-fleet automation retrofit at the $10 billion Roy Hill iron ore in the Pilbara, the Swedish manufacturer has now won its largest ever order for autonomous, electric surface drills with a A$350 million supply deal with Fortescue. Fortescue already has 190 autonomous dump trucks at its Pilbara iron ore operations.
Epiroc CEO Helena Hedblom said in a record year in 2024 for the company in terms of sales revenues and orders, “the demand was particularly strong for automation solutions, including mixed-fleet solutions”.
“At year end we had an automated fleet of more than 3450 driverless machines of mixed brands, up 21% from 2023,” Hedblom said.
Riku Pulli, president of Sandvik’s mining digital business, said last month the company’s important 2024 acquisition of Australia’s Universal Field Robots would allow it to connect more types of equipment into its 25-year-old AutoMine platform. The manufacturer had more than 1000 autonomous mining units delivered and running.
A banner site was copper major Codelco’s giant El Teniente block cave mine in Chile which had bought more than US$100 million of Sandvik automated trucks and loaders. Pulli said autonomous machines allowed Codelco to safely and economically recover one million tonnes of copper ore that had “turned to red mud [and was] way too difficult and risky to mine out” using equipment operated by people.
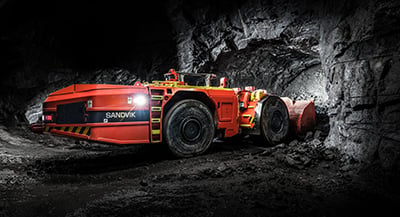
“Zero entry mining can be a viable and effective means to contribute to the demand for metals and minerals,” the Global Mining Guidelines Group (GMG) said last month when launching a white paper on future mines without people in them. New-generation autonomous equipment was pivotal.
“Being able to access deeper, complicated orebodies in remote areas without the need for people to enter the active mining areas will become essential.”
Sweden’s Hexagon says growing demand for higher productivity and product and process quality, coupled with demographic changes, is driving the adoption of automation and robotic technologies across different industries. Mining generates more than half the company’s circa-$650 million-a-year Autonomous Solutions business.
This month’s acquisition of AI-based drill automation technology in the US continues Hexagon’s mining automation portfolio build-out, which has seen it add Canada’s Hard-Line and Germany’s indurad in the past two years.
Hexagon’s mining executive vice president Dave Goddard said Drill Assist, purchased from Arizona-based Phoenix Drill Control, would “play a pivotal role in our customers’ blast planning and autonomous drilling”.
Another company adding to its auto-mining capability set is global contract mining major, Thiess, which recently formalised a partnership with China’s EACON Mining Technology in Australia.
Thiess CEO Michael Wright has said the company had been expanding its fleet of autonomous haul trucks, drills and other equipment over more than a decade.
“Though [2022 acquisition] MACA the group has progressed vendor-agnostic autonomy and electrification,” he said.
“So as a group we have a strong team and strong focus on both autonomy and electrification.
“Autonomy enables sustainable operations through enhanced safety, increased productivity and improved efficiency.”
The investment arm of $160 billion Chinese lithium battery maker CATL this month backed auto-mining technology company EACON’s latest circa-$55 million equity funding, fuelling the latter’s efforts to build a foothold in the key Australian market. CATL Capital is said to have led the series D raise by EACON, which has garnered more than $150 million of private funding as it has deployed 1500 autonomous trucks at 20-plus mine and quarry sites over the past 2.5 years.
Thiess is retrofitting trucks with Eacon control systems at gold mines around Kalgoorlie in the heart of WA’s eastern goldfields. The sites are operated by Norton Gold Fields, controlled by China’s Zijin Mining.
Continue the conversation at IMARC 2025
Thiess, Epiroc, Sandvik and Hexagon are some of the international mining autonomy leaders that will feature at this year’s IMARC in Sydney.
The October 21-23 event’s day two plenary will feature case studies demonstrating how companies are boosting productivity, cutting costs and accelerating decarbonisation through the integration of technologies such as AI, automation and asset management across mining operations.
Across dedicated Digital Transformation and Mining Innovation streams, sessions will feature technology application spotlights including the latest on AI, digitalisation, automation and robotics, and how these are supporting productivity and optimisation advances.
IMARC 2025 will also include within its Innovation & Investment Alley hosted roundtable discussions led by innovators looking to commercialisation solutions that support the future of mining.
IMARC draws attendees from more than 120 countries, with 50 nations represented at a government or ministerial level.
AusIMM members can enjoy special discounted rates - find out more and register today.