The role of mine planning in high performance
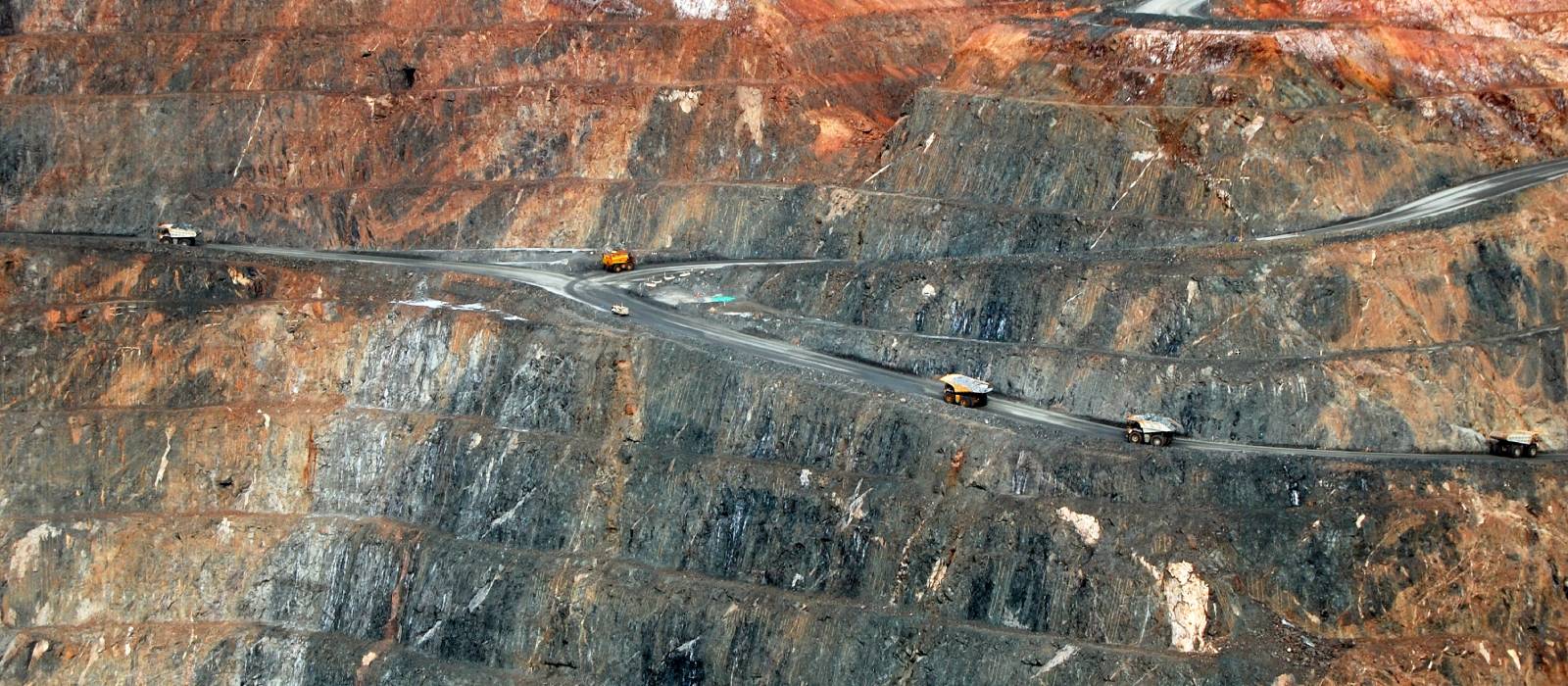
This article was published in 2015.
A holistic approach to mine planning can create value and present opportunities for both new and existing projects
Mine planning plays an often understated but nonetheless essential role in the achievement of high performance. By identifying the potential value in the given mineral resources, and providing a practical and realistic optimal strategy for extraction that considers all the material options and scenarios, a good mine planning process provides the foundation for high performance. In this strategic context, high performance is not synonymous with having a low cost per tonne or high equipment productivity, but rather it is defined by creating the most value for a mine’s stakeholders. A high-performance mine is one that has an optimised strategy and aligns its operations with strategic intent.
The reduction in mining productivity both on a volume and cost basis during the mining boom, coupled with the lower commodity prices and reduced investor confidence that has prevailed in recent years, has resulted in an industry-wide focus on increasing productivity and reducing costs. Such measures were necessary to address the rapid decline in commodity prices and investor confidence, and also the inefficiencies that had become the norm during a sustained period of high minerals prices. But it is a focus on value creation that potentially offers miners the most opportunity to improve overall performance and maintain their competitiveness.
The link between mine planning and high performance
There is a clear link between mine planning and high performance. Mining projects are unique due to their finite project life and the inherent uncertainty associated with technical factors such as the natural variability in orebody geometry and grade, ground conditions and rock properties, and the presence of different ore types and the associated metallurgical implications, to name just a few. Economic factors such as variable minerals prices and exchange rates also have major implications on the performance of mining projects. These uncertainties mean that the effective management of risk requires more rigorous economic and technical assessment than in many other industries.
Significant time is often required between the identification of a mineral resource and its conversion to an ore reserve and eventual extraction as a saleable product. Once the key strategic decisions have been made – that is, regarding the mining method, production rate, and cut-off grade (or ‘cut-off’) – it is often difficult to change the strategy. So, it is important that the strategy is sound in the long-term. Further, no amount of productivity improvement or cost reduction will maximise value if the mine plan being implemented is suboptimal.
From an operations perspective, the root cause of low productivity ‘at the face’ is often attributable to either inadequate consideration of the technical and operational factors during the development of the mine plan, or poor compliance with the mine plan. For example, it is quite common to observe a shortage of working areas at operations due to a lack of waste stripping or mine development. Measures to reduce costs, such as reducing cut-back widths and reducing or delaying mine development, can result in equipment not being able to operate efficiently due to the large number of sequential and interrelated mining activities. Further, efforts to increase productivity or reduce costs, where compliance with the mine plan is poor, can lead to the prioritisation of mining low-grade material that is readily available rather than higher-grade material that will add value.
Good mine planning leads to high productivity by both maximising the ability to work and, when work is being undertaken, by providing an environment that is conducive to high productivity. This is achieved through a combination of discipline in adhering to the mine plan, providing adequate buffering in the form of technical knowledge, ore stocks, and mining capacity in upstream and downstream activities to effectively manage uncertainty and normal variability, and enabling high productivity.
High performance is primarily achieved by ensuring that an optimised mine plan, which is both practical and achievable, is being implemented as efficiently as possible. Ultimately, the major focus of the mine should be to deliver the physical targets (such as ore tonnes and grade, waste development, and backfill) in accordance with the mine plan and within the cost and other constraints set out in the business plan. In addition, the mine’s ability to deliver its future key performance targets should not be compromised.
Developing the optimal mine plan
To develop the optimal mine plan, first it is necessary to define the measures of value that represent the corporate goals. Net Present Value (NPV) is the most common parameter considered when undertaking project evaluation and determining strategy. Most companies, however, have multiple, and often conflicting, corporate goals, so other measures are frequently evaluated.
It is noted that most feasibility studies and life-of-mine or expansion plans merely demonstrate that a particular option for project development is technically and economically viable. If the project as defined by the study is apparently healthy and robust, there will typically not be any attempt to find a set of options that provides a significantly better outcome. Although it is common to hear that a project being developed after a favourable feasibility study is being ‘optimised’, this typically takes the form of finding better or cheaper ways of implementing the strategy identified by study. It rarely seeks to find a different and better strategy, or one that creates the most long-term value over the range of likely economic and technical scenarios. Most mine plans are therefore based on a strategy that has been (at some time, but not necessarily recently) demonstrated to generate an acceptable positive NPV, but not on a strategy which has been demonstrated to maximise NPV or any other measure of ‘value’. Minimisation of risk may be considered qualitatively, but it is rarely quantified and included in the formal determination of the ‘best’ option. This is unfortunate given the uncertainties surrounding mining projects, particularly if evaluation is conducted at the peak of the mineral price cycle. It may help to explain the rapid expansion at any cost which invariably occurs during such peak periods.
The ‘Hill of Value’ approach to mine optimisation
The ‘Hill of Value’ approach to mine optimisation has been developed to enable the identification of the optimal mine plan.
The mine optimisation process using the Hill of Value approach is in principle no different from any other life-of-mine study that a technically competent mine planning team would conduct, except for the large number of combinations of mining options tested under a comprehensive range of input scenarios. This approach allows a thorough and rigorous assessment of the various options under the full range of likely scenarios to be investigated, and allows a robust ‘optimal’ solution to be identified.
To achieve this, the Hill of Value evaluation model needs to be substantially more flexible than those typically used for a ‘single scenario’ study. As with any study of this nature, various levels of detail and accuracy may be specified. Typically, a less accurate higher-level study may be conducted first to identify the most likely value maximisation strategies. This may be followed by a more detailed study of a smaller number of options if deemed necessary. Figure 1 is a Hill of Value from a real study, and it demonstrates the concepts of the technique.
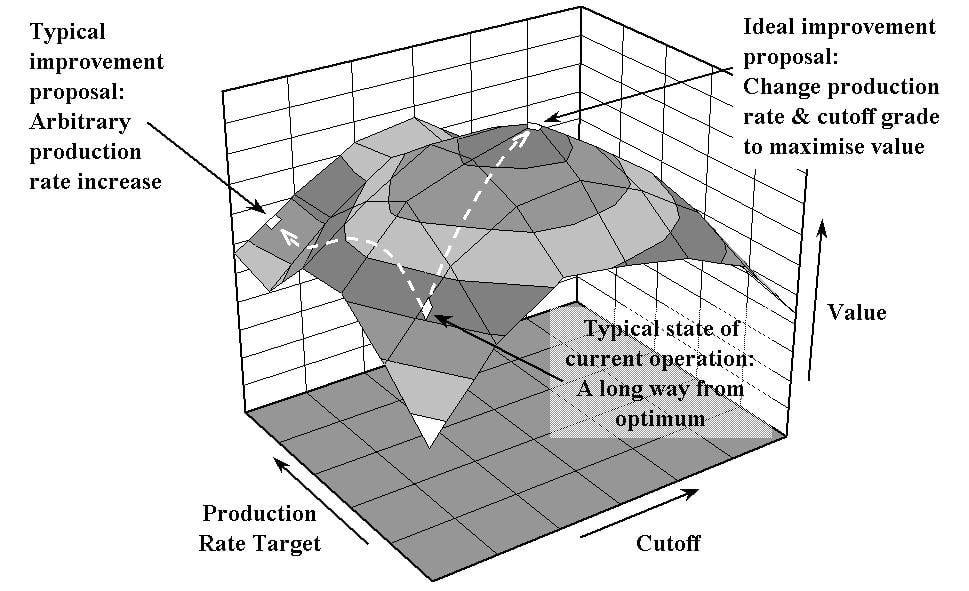
The importance of cut-off grade
For a given mineral deposit in a given social and economic environment, and with the existing infrastructure, the major parameters that a mining company can make independent decisions about are typically the mining method(s), mining sequencing, production rate, and cut-off. Since the size and shape of the orebody and hence possible mining methods and the range of feasible production rates may vary significantly with cut-off, it is often the cut-off that is the key driver of value of the operation.
Once decisions regarding cut-off (and mining method and production rate) have been made, most other factors are then to a large extent determined. Physical factors such as mining layouts and treatment plant design, and the capacities of various stages of the production process from mine to market, will be known. Resulting from these are financial factors such as initial or expansion capital expenditure requirements, staffing requirements, and all the various components of the operating cost structure.
Mine optimisation should be conducted as early in the mine-planning process as possible to minimise the risk of locking in a suboptimal plan and losing an opportunity to create value.
Study components
The following discussion summarises key aspects of various study components, with particular reference to how they may need to be handled for an optimisation and risk management study where this differs from a typical single or limited scenario study. These matters are discussed in more detail in Hall and Hall’s 2006 Doing the Right Things Right – Identifying and Implementing the Mine Plan that Delivers the Corporate Goals.
Geology
A reasonably reliable model of the mineralisation for the range of cut-offs to be investigated must be created.
Mining parameters
Having acquired a suitable geological model, it is then necessary to generate orebody outlines at each cut-off. For an underground mine, it is necessary to identify suitable potential mining methods at each cut-off. Realistic mining shapes can be designed for each of these. For open pits, bulk or selective mining methods may be indicated at different cut-offs. Conceptual mine designs and schedules must then be developed for selected representative cases.
Metallurgical parameters
Recovery relationships must be specified for the range of cut-offs to be evaluated. Other parameters that may vary with treatment plant feed quality may need to be identified. Constraints at various stages of the metallurgical process need to be specified, along with the actions required to remove them.
Operating costs
Several different categories of costs need to be identified, together with the physical parameters, or cost drivers, on which they depend. Fixed and variable cost components and their physical drivers over the full range of activity levels to be investigated must be identified.
Sustaining capital costs
Several different types of ongoing or sustaining capital expenditure may need to be identified and handled appropriately.
De-bottlenecking or project capital
This is typically proposed to increase capacity in some part of the production system, or to improve product quality. Project capital expenditure should be justified on the basis of the difference in maximum values obtainable with and without the expenditure, and not on the basis of the difference in values at a fixed cut-off or production rate. Failure to recognise this principle may result in loss of potential value or increase in financial and economic risk.
Risk analysis
Once a suitable evaluation model has been developed, it can be used to generate much more useful information than just Hills of Value. It becomes a significant risk assessment and management tool for project viability and profitability.
The trade-off between risk and reward
Figure 2 shows Value vs Cut-off curves for two different metal price predictions. What cut-off strategy should the operation adopt? The temptation is to select the cut-off that maximises the value at the higher price, since this clearly maximises value overall. However, the figure shows that if a higher cut-off to maximise value at the lower price is selected, and the higher price then occurs, most of the potential increase in value is obtained anyway. The real gain obtained by selecting the lower cut-off (to maximise value with the higher price) is in fact quite small. But if the lower cut-off that maximises value at the higher price is selected, and the lower price then occurs, the loss may be substantial. Typically, the lower the cut-off selected, the greater the risk.
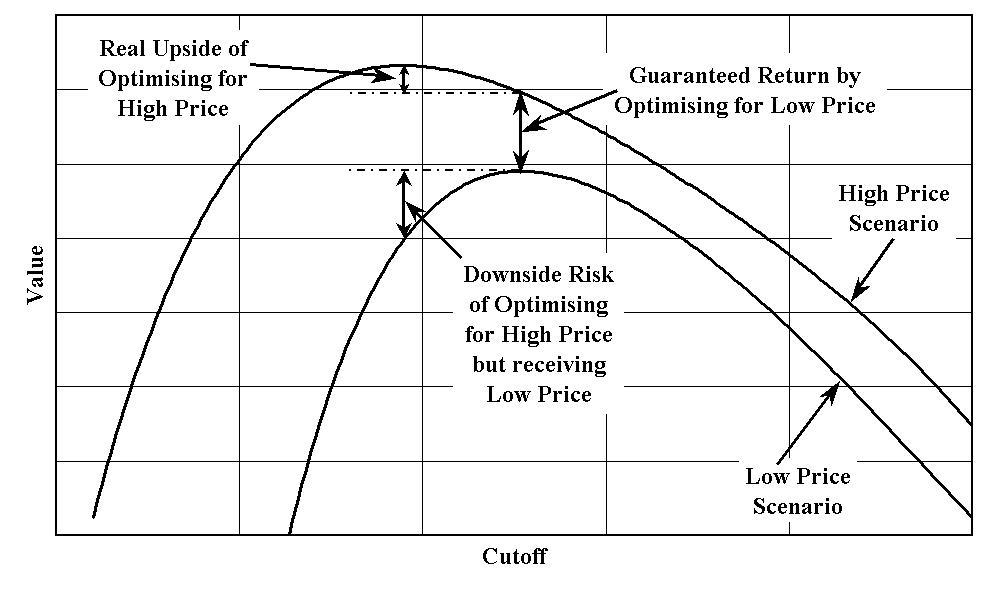
The trade-off between risk and reward evident in Figure 2 and will be dependent on the shapes of the Hills of Value, and these will obviously vary from project to project. The magnitudes of the risks and rewards flowing from cut-off policy selection have a direct and major impact on the value and financial strength of the company, and must be a matter for board consideration and decision-making.
Efficient implementation of the optimal mine plan
A comprehensive and integrated mine planning process is essential to the development, and efficient implementation, of the optimal mine plan. The process should encompass strategic, business and operational mine planning and fully integrate all stakeholders – including management, geology, mine technical services, processing, maintenance, and production – such that the operations are aligned with the optimal mine plan.
To achieve the desired outcome, mine planning can be considered on three sequential, but integrated, levels:
- Strategic planning: an overall plan to maximise the value from the exploitation of the known and anticipated mineralisation. This should identify the optimal mine plan.
- Business planning: comprising two components – long-term and medium-term planning, both linked to the strategic plan but more detailed. Typically business planning incorporates the annual budget through to the five-year business plan.
- Operational planning: detailed plans – including the rolling three-month forecast and monthly, weekly and daily equipment plans – which guide the operation to achieve the business targets detailed in the budget.
To ensure that the mine plan is practical and reasonable, a good mine planning process is aligned throughout and incorporates comprehensive technical knowledge and extensive interaction with the various technical disciplines and stakeholders. The detailed inputs and interactions will vary depending on the level of detail of the mine plan under preparation but broadly will entail management, geology, geotechnical, metallurgical, marketing, maintenance (fixed and mobile plant), infrastructure, production, mine technical services, and social and environmental considerations. The primary objective of a good mine planning process is to direct the implementation of the optimal mine plan, as efficiently as possible.
A good mine planning process makes effective use of the rapidly developing mine planning software that enable mineable shapes to be rapidly developed, schedules to be readily updated, and numerous options and scenarios to be evaluated relatively quickly. The increased integration between the mine design and scheduling software also readily allows visual inspection and interrogation of the mine plan. However, the limitations of such software tools must also be understood. For example, all mine planning tools have strengths and weaknesses, with some better suited to strategic applications and others more suited to the development of detailed operational plans. The best results are achieved by selecting the most appropriate tool for the specific requirements of the mine plan being prepared, rather than using a one-size-fits-all approach.
Introducing a rigorous mine planning process that is aligned with the mine operations will often lead to reduced variability, and also volatility. Thus, while productivity and efficiency improvements may be the best way to reduce costs in the short-term, such measures should not compromise compliance with the mine plan.
Compliance with the mine plan is critical to value creation. Reconciliation between planned and actual performance should be regularly measured and monitored. Non-compliance should be critically reviewed by all stakeholders and appropriate actions should be taken to minimise future deviations, and where necessary re-calibrate the mine plan if greater knowledge results in material changes to input parameters.
The monitoring of compliance with the mine plan should consider spatial as well quality and quantity aspects. It is important to identify where material has been mined to facilitate thorough reconciliation and to ensure that the progress of mine development, which enables access to future ore sources, is adequate to meet longer-term strategic targets.
Conclusion
Value creation through the development and efficient implementation of an optimal mine plan is a major opportunity within the mining industry today. The concepts presented above are not new or indeed particularly innovative. However, a holistic, rigorous, disciplined and integrated approach to mine planning, as described, can transform mining operations and create value. This is true for existing projects as well as new projects.
The establishment of good mine planning and related technical practices is an essential component of a high-performance mine – and it is an area that the authors believe that the minerals industry, in general, is not exploiting to its full potential. In some cases, there are gaps in understanding the driving factors behind developing an optimal mine plan that truly maximises value. In other cases, there might be a robust plan in place, but it is not implemented effectively.
Aligning mine operations with an optimised mine plan provides a substantial opportunity to create value and achieve a sustainable competitive advantage within the minerals industry. AMC can assist in this area, with its considerable expertise in all facets of mine planning and well-established tools for diagnosing gaps in mine planning processes and identifying potential areas for value creation (such as the Hill of Value approach outlined in this article).
References
Hall A and Hall B, 2006. Doing the Right Things Right – Identifying and Implementing the Mine Plan that Delivers the Corporate Goals, in Proceedings International Mine Management Conference 2006 (The Australian Institute of Mining and Metallurgy: Melbourne).
Hall B, 2014. Cut-off Grades and Optimising the Strategic Mine Plan, Spectrum Series 20 (The Australian Institute of Mining and Metallurgy: Melbourne).