Automation in mining – current and future opportunities
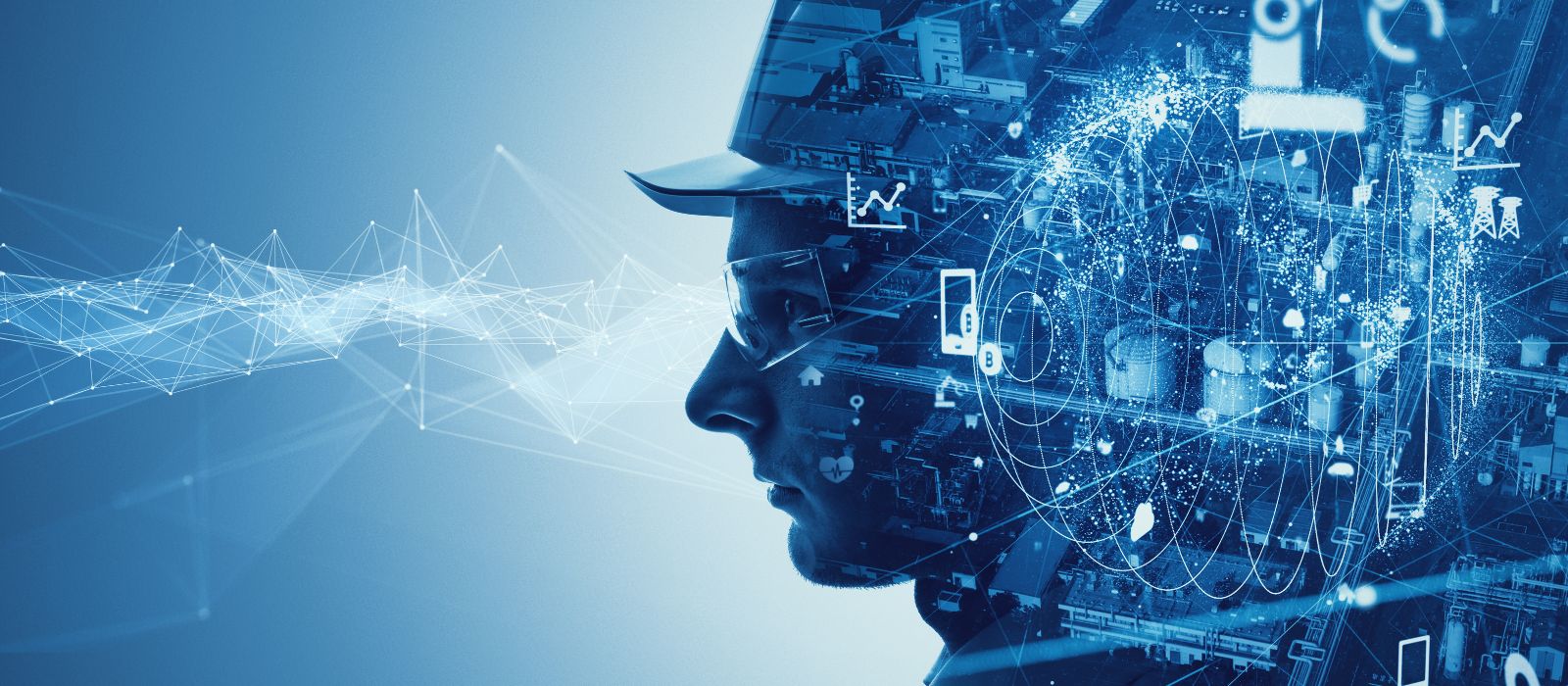
Automation is changing the industry – but what does it mean for resources professionals?
We caught up with Jonathan Weidenbaum, Principal Automation Consultant at Emerson Automation Solutions, to discuss the changes that have taken place in process plant automation technology, the benefits automation can bring, and how these new approaches can help ‘future proof’ projects.
You have more than 35 years’ experience when it comes to automation and project consulting. What do you see as the biggest change since you started your career? Did you imagine that the technology we have today would be possible?
The changes in technology I have seen in my career have traditionally followed a cautious evolutionary path. This reflects the risk-averse nature of plant owners towards mission critical systems.
However, there have been some disruptive technologies and processes that have deeply impacted the way modern process plants are built and managed. The biggest change I have witnessed is the move towards globalisation in execution, where construction sites become a staging area for multiple packages that converge from across the world – exposing interoperability as the major schedule and budget risk.
The drive towards globalisation requires an agile approach to project management, utilising global and local resources, and leveraging virtual office toolkits to provide global engineering collaboration. This emergent need requires intercontinental networking and digital twin infrastructure to enable remote factory acceptance testing at the fabrication yards.
Getting this right requires teams with global reach and support. But when it is right, this approach can realise substantial benefits, potentially reducing the commissioning period by months and accelerating the operating plant towards top quartile performance in a much tighter timeframe.
The other major change I have seen is the adoption of advanced and predictive analytics migrating into real time operations. This is used for process optimisation, attaining the gold standard of autonomous operations together with predictive maintenance, encompassing the complete value chain into the automation system. These benefits are traditionally expressed in terms of increased production, enhanced product quality or reduced OPEX. However, today, the emphasis is on decarbonisation and how these operational efficiencies can contribute to reducing the carbon footprint.
The infrastructure to support this higher level of automation and efficiencies has led to the adoption of pervasive sensing, cloud-based data access, and the use of powerful analytic engines and digital twins to improve plant performance, reduce emissions and extend asset life.
You have been involved in projects for the oil and gas sector where automation is used for remote site monitoring, eliminating the need for technicians to travel to site to take readings. Is this kind of approach viable or useful in the mining sector?
Absolutely, the main driver for remote operations is health and safety to reduce windscreen time and remove people from hazardous environments.
There are obvious cost benefits from moving to remote operations, but the primary goal is to improve safety and performance while maintaining consistent product quality. To achieve true autonomous operations, the technology and philosophy needs to be applied to the complete operational model. This includes operations, integrity, asset maintainers, housekeeping and equipment specialists.
The technologies and processes need to be considered up front and not applied as an afterthought; ad-hoc and scheduled visits need to be reviewed and assessed and every manual activity mitigated with an automated technology. This includes substituting visual inspections and security checks with CCTV and cameras, asset inspections with online condition-based monitoring, consumables checks with pervasive sensing, operation intervention with automated decision support, or remote located fixed asset inspections with drones or satellite photos.
Unless all activities are addressed, then site visits will become inevitable and workloads will accumulate to justify the visit. The large mining companies already deploy remote operations, but this is subtly different to autonomous operations as this only transposes the decision making – not the operational physical activities.
What new approaches or technologies are being used on mine sites? Are there exciting developments or breakthroughs on the horizon?
In the previous question, we discussed the mining industry's move to remote operations; however, the gold standard for operational excellence is autonomous operation. This approach elevates the operational model to remove human intervention from automation and decision-making with advanced analytics and machine learning to provide fully automated decision making or decision support.
These technologies have already been used for offline analysis for operational refinements, but today these advanced smarts are moving into the real-time decision making realm. For example, the move towards online high-fidelity digital twins will lead to more efficient operations with enhanced capacity-based control, and see stockpiles removed from the supply chain. Machine and deep learning technologies will permeate the plants of the future, extending the remaining useful life of assets, reducing downtime and refining automated operational performance.
In essence, current technology islands and silos will gravitate towards a seamless, interoperable, business-wide, autonomous value chain management system.
How do resources professionals fit into an automated mine site – what skills do they need and how does their ‘traditional’ role change?
Over the years I have had the opportunity to visit educational centres for process automation and observe how our operators and engineers are still being trained in a control-room centric, reactive environment. In the future, equipment and mining specialists will go to site for predictive purposes only; ie to address “tomorrow’s problems”. The performance refinements (ie “today’s issues”) will have already been avoided. There will always be a need for reactive/scheduled activities for unforeseen events, but these will be in the minority.
Typically, future professionals will not need to go to site, and unfettered access to data will be available through pervasive sensing and cloud-hosted systems. Data analytics will be readily available and decision support and predictive analytics will define when someone is required on site, at the right time, with the right equipment and the right spares. Once there, wearable technologies enable the onsite personnel to work in a collaborative manner with online connected experts.
What are some of the ways that automation can help improve overall ESG outcomes?
Automation and ESG outcomes are already interwoven to a large extent, as compliance to the objectives of ESG makes good business sense and brings reputational benefits. The intolerance to waste, emissions and the drive to efficiency and sustainability are the new pillars for social license and responsible business.
How this translates into effective automation initiatives is based around process and combustion efficiency programs, substitution of hydrocarbons with blended biofuels or hydrogen, introduction of renewables into the plant microgrid, and good energy management and housekeeping.
What do you see as the challenges to future proofing new greenfield sites?
The main challenge in developing a technology roadmap is resisting the decoupling of the OPEX and CAPEX initiatives. Typically, on greenfield mining projects, the initial project development focus is fixated on the CAPEX investment, ignoring OPEX optimisation opportunities during Front-End Engineering Design (FEED) or removing them in the first round of CAPEX rationalisation. This will typically mean that the plant will not achieve top quartile performance for several years after commissioning handover. The cost impact of this approach is staggering and can represent over 25 per cent of the original CAPEX in lost opportunity.
So how can you ensure that your plant is ready at commissioning and will achieve or exceed the performance expectations from day one of operation? One area we have seen great benefits is in the selection of your technology partner as an early contract engagement. Automation of the plant represents only a small part of the CAPEX budget but will be critical in the success and viability of the plant. Selecting your technology partner up front will streamline the design and execution process and will enable the operator to leverage the vendor’s experience and knowhow into the design process mitigating well known schedule and project risks from the automation perspective.
Another essential consideration during FEED relates to the operational model selected. This needs to be agile and capable of evolving with the technology innovations deployed to site. There are many examples where proven technical innovations do not deliver, as the business processes have not developed around these new technologies to leverage the expected outcomes. Agile solutions require agile operations. Again, early engagement with the technology suppliers can help the end user prepare their operational readiness plant to deploy and exploit the benefits of autonomous operations, predictive maintenance, continuous performance improvement, asset life optimisation and enhanced ESG targets.
Looking ahead – what do you think the future holds? Where will we be in another 30 years?
Predicting the next 30 years in automation sounds like a plot for a science fiction movie, but 30 years is a typical operational life of a greenfield plant. The trajectory for that vision of the future is already set in the design of today’s plants that are emerging off the drawing board, although this is not readily appreciated.
The key question for a projection into the future, other than the relevance of the market and product, is what will staffing levels be, will there actually be people on site, should the design be human-centred or designed around autonomous operations. If the answer to these questions is a vision of full automation, then do you need aspects of life and comfort support systems such as canteens, offices, walkways, air conditioning, accommodation or should remote autonomous operations be the foundation of design?
Then there is consideration of the future advanced business operation and analytical systems, and how all these inevitable disparate systems that contribute to the operation of the business can be consolidated into a fully interoperable and close coupled business and market management system.
There is no immediate capital commitment required now to set the trajectory to this vision, but there does need to be careful considerations of technology and infrastructure to enable this to eventuate. These include adopting onsite open standards incorporating network, electronic marshalling, on premises controllers and edge controllers, adoption of wireless sensing together with a secure but open standard backhaul connection to remote operations centres, collaboration centres and cloud based corporate data lakes.
This early consideration to open standards will facilitate direct interoperability of the company operations, maintenance, analytics, business improvement and financial systems. Once these systems are humming together, this will realise the vision of a fully autonomous supply and value chain operation.