Barriers to innovation in mining and ingredients for success
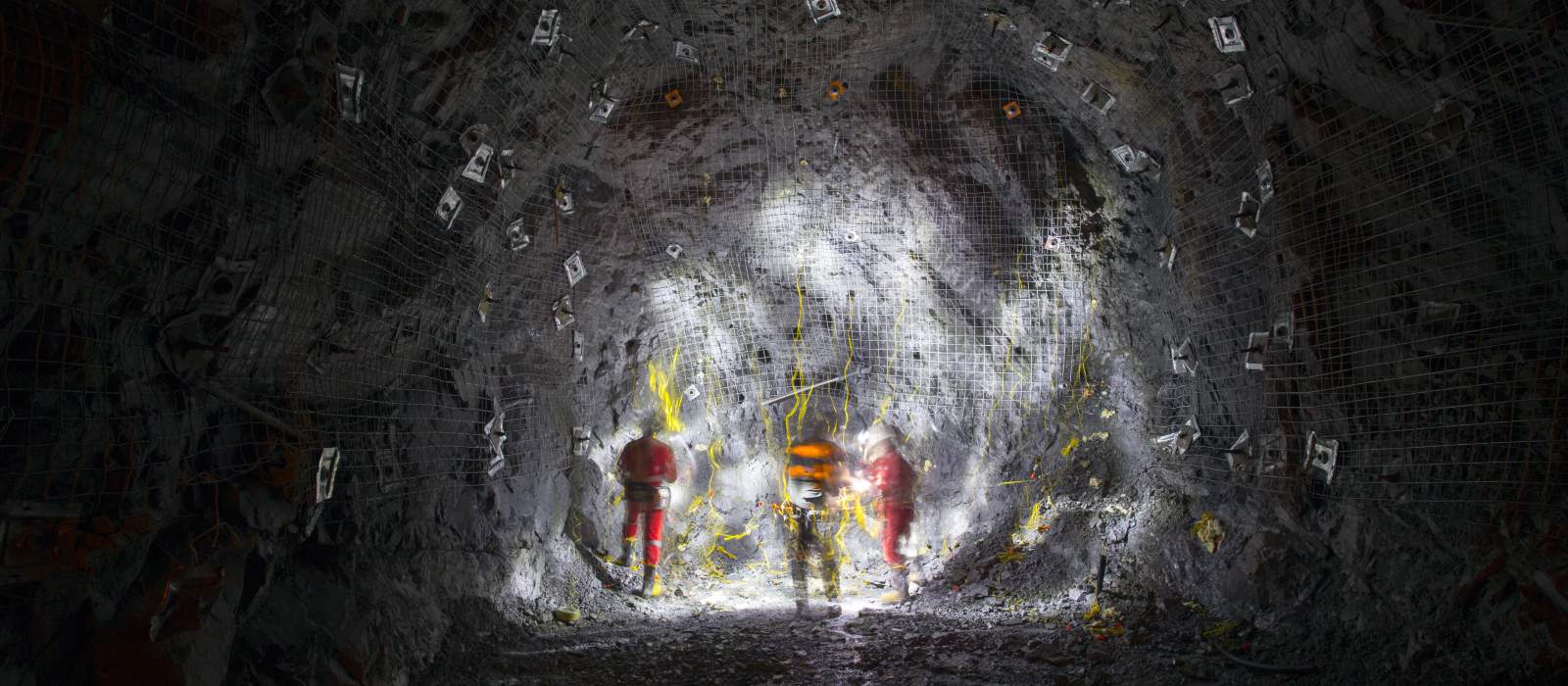
Realising the benefits of innovation is easier said than done, with several barriers standing in the way of successful implementation. But if mining companies were to focus on six ingredients for success, the innovation path could become a little easier and faster.
Innovation in mining is a topic that can be divisive, as ‘innovation’ invariably means change: change to what we do and how we do things. A human characteristic of this is that we often don’t deal with change well. People within the mining industry generally fall into two camps: the first are those who are amazed at all of the new technologies and ways of doing things differently; and the second group are those who are deflated, thinking we haven’t really fundamentally changed what we do, and find changing anything hard and slow.
What do we mean by innovation?
Innovation often gets conflated with business improvement. What I mean in this article by innovation is doing things in fundamentally different ways, not just doing what we currently do faster, better, and/or cheaper (that’s not to say business improvement is bad, it isn’t, but it also isn’t innovation).
Matt Ridley in his recent book How Innovation Works (2020) talks about innovation as ‘a process of constantly discovering ways of rearranging the world into improbable forms that are unlikely to arise by chance and that happen to be useful; the resulting entities are the opposite of entropy, they are more ordered and less random than their ingredients were before.’ Ridley goes on to say that ‘innovation means much more than invention, because the word implies developing an invention to the point where it catches on because it is sufficiently practical, affordable, reliable, and ubiquitous to be worth using’. Ridley also quotes Austrian economist Joseph Schumpeter, who said in the early 1900s, ‘Innovation offers the carrot of spectacular reward, or the stick of destitution.’
So the stakes are high, and there is often a long and tortuous journey from idea to innovation and then to ultimately realising the benefits.
There is a view that mining is slow to innovate. This assertion is often made when we compare mining to other industries such as manufacturing, transport, pharmaceuticals and even agriculture. One could take the view that mining has barely changed in the last 50 to 100 years.
Why does mining have a slower rate of change and innovation than other industries? The mining industry is not short of ideas, yet we continue to see a very slow take up or even the ignoring of what seem to be obvious value-adding opportunities. We see companies undertaking test after test, carrying out pilots that even when they are successful go no further, or we see one pilot after another, referred to as ‘pilot purgatory’.
The industry is often accused of being overly conservative or risk averse, although the real reasons are a lot more complex than this.
To explore this further, I want to first focus on four barriers that I am suggesting regularly get in the way of, or slow down, innovation. Some of these barriers are unique to the mining industry. Then I will describe six ingredients that I believe are necessary for successful innovation.
Take note that none of these barriers or ingredients for success have anything to do with the technology itself. They are instead all focused on people, organisational aspects and the choices we make. For the most part, they are all in our control.
Barriers getting in the way of innovation in mining
1. The cadence of the mining industry
The cadence of the mining industry is different from other industries. Manufacturing tends to work on a cadence driven by a product cycle, and product cycles have been getting shorter. Agriculture works on a seasonal cadence. The semiconductor industry works to a cadence defined by the size and number of the transistors they can engrave on silicon (further explored in Moore’s Law).
Mining, on the other hand, has a cadence built around the orebody. Miners usually only get one chance to build a mine for a particular orebody, and to choose the key technologies, the mining method, the flowsheet, the equipment and the layout. From that point on, the way the mine operates is set in concrete (literally), the mine operators are destined to just tinker around the edges to incrementally improve it.
Our inability to change these fundamental choices later is made worse by the mining of high-margin material early in mine life, leaving low margin material that often won’t justify re-capitalisation later in the mine life. Exacerbating this is the cyclical nature of commodities, swinging from boom to bust. When in boom there is the need to add new capacity rapidly, which means low risk, which in turn means use existing proven technologies.
2. Proprietary approaches including intellectual property protection
Evidence shows intellectual property (IP) protection does more to hinder innovation than help it. It slows the flow of ideas into application. The whole idea, of new ideas, is to share them and allow them to be copied. There is an inverse relationship between the number of patents a company has, and the amount of innovation they are doing. This invariably leads to a significant waste of energy and money on protection. Bursts of innovation occur at points in time when patents expire. Relying on first mover advantage would instead lead to the speeding up of innovation.
In the mining industry we have seen closed and proprietary approaches, particularly from the major original equipment manufacturers (OEMs) and suppliers, that has led to major barriers to the industry moving forward in areas of systems and data integration. This is preventing the interoperability of equipment as we attempt to automate mines and as we try to move toward the vision of zero-entry operations. This proprietary approach is slowing innovation in mining.
3. Wrong people in wrong roles – the artists and the robots
In his book Loonshots (2019), Safi Bahcall describes the fragility of innovation, and the role the inventor or innovator plays. Bahcall calls the innovators ‘the artists’, characterised by being divergent thinkers, creatives, curious and experimenters. He then describes the role of the people in operations, who must be structured, follow defined processes and reduce variation. He calls these people ‘the robots’.
A successful organisation must have both artists and robots. It needs to have them in the right roles, doing the right things. Artists need to be protected and incentivised very differently to robots. The transition between artists and robots needs to be carefully managed. Too often in the mining industry we find artists the victims of the cycles or they are forced to behave like robots – we all know how that ends up. Likewise, don’t ask a robot (or operations person) to be creative and experiment; it is not good for them or for the operation.
4. Organisation or operating models
There are two aspects to discuss here. Mining companies are often run as a series of very independent businesses where the General Manager is fully accountable for everything that goes on (they are the King of their Fiefdom). The corporate centre in these cases has very little say, even in the selection of equipment, processes or technology. This worked in the past but severely limits innovation in the digital age. Much of the digital innovation relies on common equipment and standard processes, such that new ideas can be implemented and then scaled at close to zero marginal cost. Other industries have dealt with this long ago and have a far more sophisticated approach to what needs to be tightly controlled by the enterprise and what is for the site management to decide.
The other operating model that impacts innovation is the use of engineering, procurement, construction management (EPCM) contractors for major project development and construction. I believe this is responsible for a significant negative impact on greenfield mine developments. At the very time when you are making all of the key decisions that the mine will have to live with for its life, we employ third parties to design, engineer and construct these mines, thus outsourcing the key decisions.
Worse still, these third parties are given incentives to deliver on time and budget and have their final payments contingent on proof of production capacity. These incentives do influence their decisions, biasing them against anything novel or new, and causing them to prefer the old ‘tried and proven’ methods. This approach also biases mine and plant designs to be over capitalised so they can meet their production test earlier. The key question that needs to be asked is: ‘are we building tomorrow’s mine today, or yesterday’s mine today?’
These are the barriers that get in the way of innovation.
Ingredients for successful innovation in mining
According to Matt Ridley again ‘The main ingredient in the secret sauce that leads to innovation is freedom: freedom to exchange, freedom to experiment, to imagine, to invest and to fail.’ So how do you think the mining industry stacks up with these ingredients?
While the act of inventing something or innovating is serendipitous in part, any organisation needs to set themselves up to be in the innovation game and give serendipity its best chance.
I propose that there are six important ingredients that mining companies who want to be successful innovators need to have or do.
1. People
Employees at all levels have a part to play. They don’t just need to know and understand what is going on, they need to understand why things are changing. They also need to know how the change impacts them, their role and what is expected of them in future. It is a natural human reaction to be suspicious or resistant to any change. A paradox that is often missed is that the higher level of automation achieved, the more important the people aspects become! It is the people that drive success or failure, rarely the technology.
2. Organisational alignment
If a company is going to be innovative, then innovation needs to be part of the DNA for the whole organisation. There needs to be consistent messaging followed through by action. Many mining companies use fancy words in their shareholder reports that don’t bear any resemblance to what is going on at the mine face. Or they have fancy strategies in the corporate office but no process or plan to actually implement anything. Worse, the message says one thing, but the KPIs and incentives say another.
People working in the organisation pick up on these inconsistencies. A lack of alignment creates confusion, friction and resistance to change; it is disempowering and demotivating, particularly for those trying to innovate. The operators are often blamed for being reluctant to take on something new, but if their measures and rewards are examined they are commonly about safety, volume and cost in the short term with no mention of doing things differently or inducing change in the longer term. Where is the incentive to try something different?
3. The structure and operating model
Mining companies need to be set up to enable the rapid take up and scaling of innovation. There needs to be clarity around who makes the key decisions, what is driven centrally and what can be delegated to local management. Early stage innovation needs to be protected and separated from operations, followed by an intentional and gradual process of transition to operators as the innovation proves to be value adding and safe. The operators should not have the opportunity to opt out and should be incentivised to make it work.
In addition, companies should ensure the critical decisions in greenfield projects are being made in their best long-term interests and ensure the mine is set up for operational success throughout its life – not just in construction and commissioning period.
4. The process matters
To be successful at innovation, a company needs to have an innovation process and this process needs to be managed. The tried and proven method is to use Technology Readiness Levels (TRLs – either the 7 or the 9 scale ones) and at the end of each level there is a rigorous stage gate process that ensures most innovations fail and fail quickly.
The TRL approach allows organisations to separate the work on the early TRLs away from operations and then have a structured way of running pilots, then trials, then moving into implementation at one operation before scaling to all operations. Everyone in the organisation needs to be clear on what stage each innovation is up to, and what it needs to be achieved to successfully make it to the next TRL. As an innovation matures, the responsibilities for managing the innovation must change.
5. The artists matter
Mining companies need the artists – the creatives and inventors – but these people need to be protected both during the cycles and within the organisation. Artists need a structure that separates them from operations and allows them the freedom to experiment and carry out the early stage innovation well away from the operations. They do need access to operations to observe and collect data and understand the operating issues, but they also need time and space to think, to experiment, and they need the freedom to try things out at small scale. They also need to be able to fail. Only when they have something that is advanced enough should it transition into trials at operations involving ‘the robots’ or operators.
6. Leadership with the courage to follow through
Organisations and particularly leaders must have the courage to follow through, implement and then to scale. Often mining companies and their leaders lack this courage. When trials have been successful, and the business case is proven, it has been too easy for leaders to opt out, delay or call for yet another trial. Likewise, we have often seen mining companies implement technologies in one mine and reap significant benefits but then fail to implement or scale to its other operations.
Realising the benefits of innovation is much harder than most people think. If mining companies were to focus on these six ingredients for success, the innovation path might just become a little easier and faster.
Innovation requires an intentional approach that is organisation wide. It also requires us to address some entrenched thinking and approaches. Some of these are at industry level and they are holding us back.
What is required is inspired leadership from all levels, to see the potential, to remove the barriers and ensure all the ingredients for success are in place to turn all of the great ideas, most of which already exist, into a reality – and then the benefits will flow.
References
Bahcall S, 2019. Loonshots: How to nurture the crazy ideas that win wars, cure diseases and transform industries (St Martin’s Press: New York).
Ridley M, 2020. How Innovation Works (4th Estate:London).