Digital transformation for minerals processing: the fundamentals (Part 2)
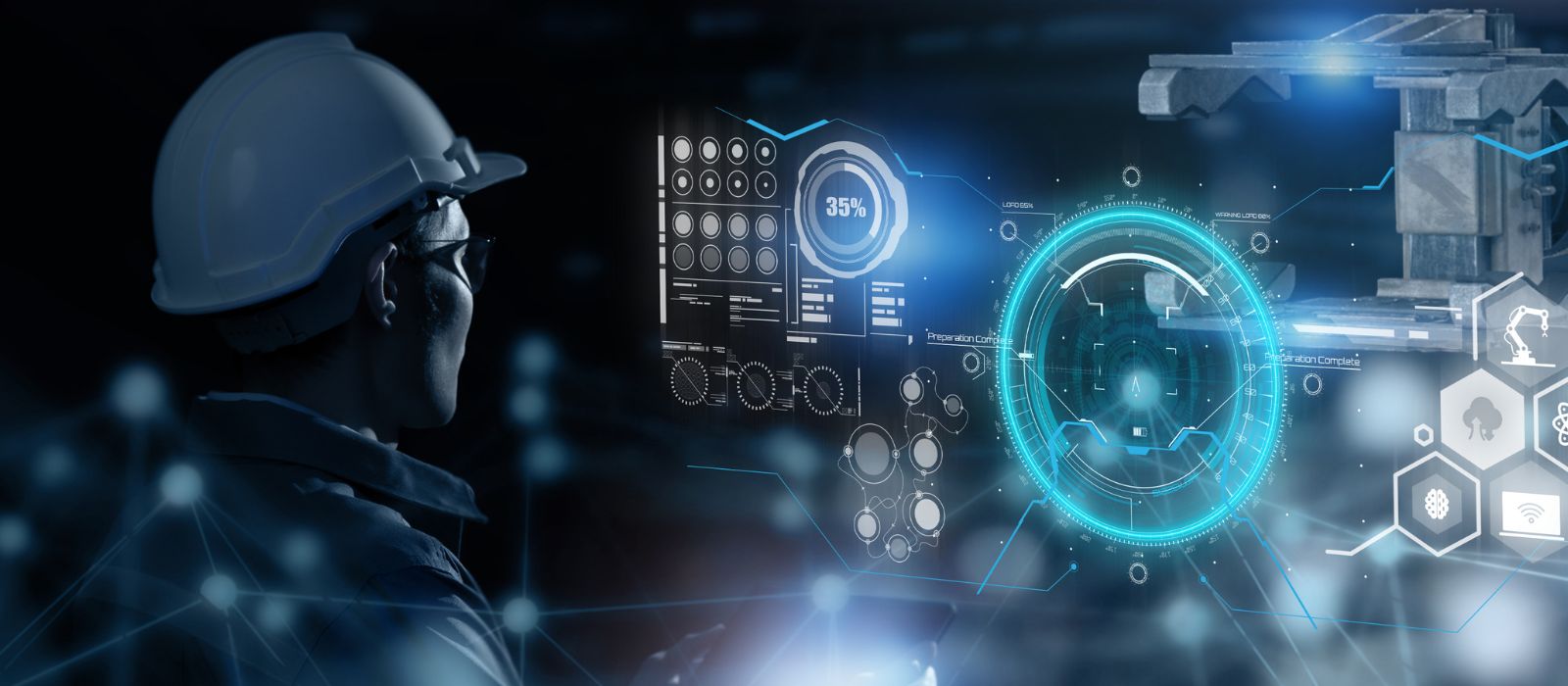
This article discusses the different types of digital twins available in the mining sector, and why a digital twin-enabled Manufacturing Execution System (MES) is vital for the effective transformation of minerals processing plants.
As discussed in the first article in this two-part series, the digitisation of the mining sector is well underway. However, the minerals processing segment of the mining value chain is often neglected – either poorly managed using dated Microsoft Excel spreadsheets, or serviced by catch-all digital solutions that lack the sophistication or nuanced insights that minerals processing requires.
In this article we provide an overview of what effective digital twin technology looks like for minerals processing.
The digital twin: a recap
There are two distinct types of digital twin solutions used in mining.
The first is the asset digital twin. This is essentially a digital replica of a physical component of a mine, developed using CAD modelling. This helps stakeholders visualise a facility when working from a remote location; for example, the use of a 3D model for mine planning such as pit designs, haul routes and mine layouts.
The second and far more sophisticated type is the process digital twin – a digital replica of the actual processing of the orebody for a minerals processing plant, from raw material to finished product. This type of digital twin uses dynamic simulation and considers a range of physical properties, such as temperature and pressure, combined with the specific chemical equations and processes that occur at each step of the refining process.
This type of digital twin can be referred to as a digital twin-enabled Manufacturing Execution System, or MES. This is a piece of software responsible for gathering, integrating, validating and centralising source data, as well as making this data available to stakeholders through analytics and visualisation tools. A high-quality MES will source data from across the plant and all levels of the automation pyramid (Figure 1).
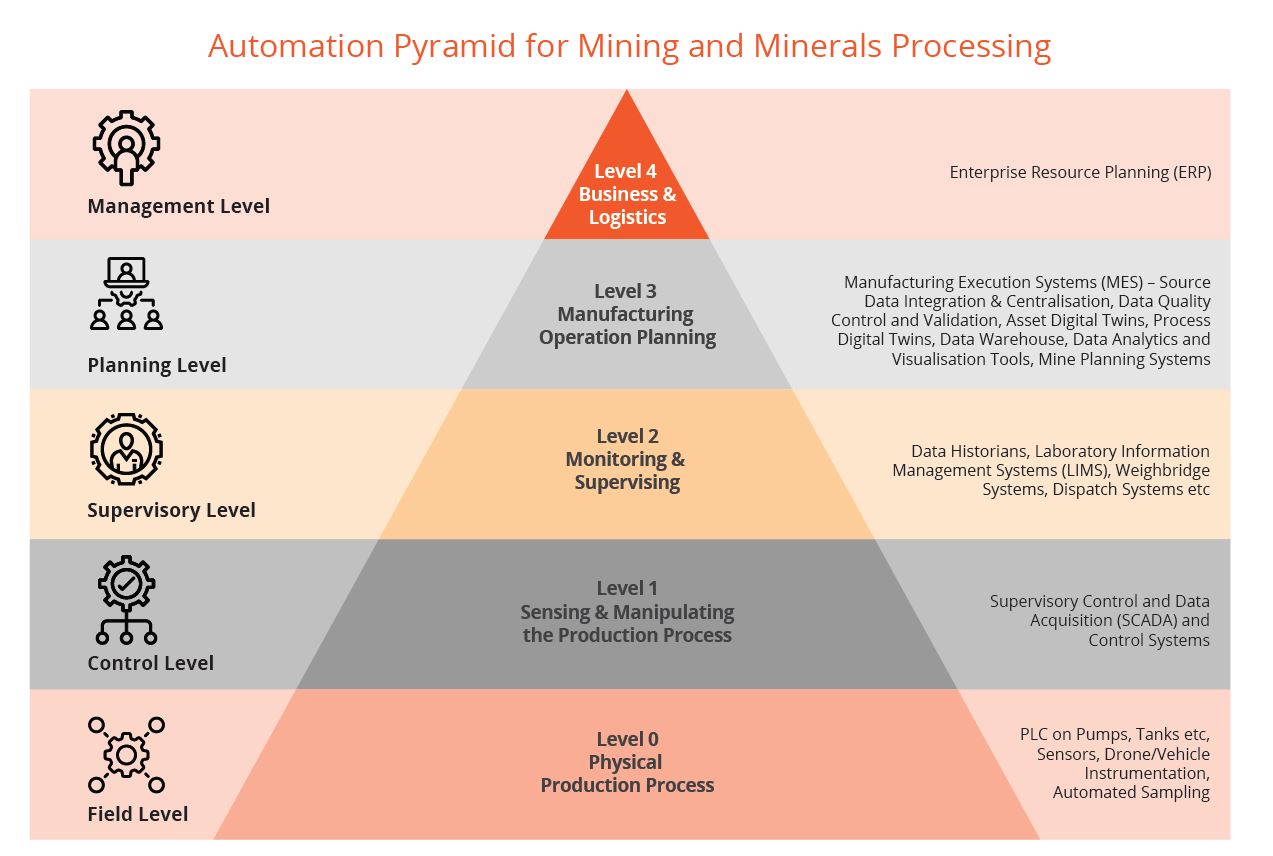
Five tips for MES best practice
There are typically five components of a sophisticated and purpose-built digital solution for minerals processing.
1. Centralised source data
Often, processing plants operate using data from disparate systems, with no ability to cross-reference or check information easily and accurately. Many plants are still reliant on manually entered data stored in spreadsheets.
The first step in digitally transforming minerals processing is to centralise and digitise data from multiple sources across the plant. This data needs to be fully traceable (so if an issue or anomaly is identified, it can be easily determined) and offer a single, organised ‘source of truth’ for authorised stakeholders.
Interoperability is a key priority: you need to ensure you are extracting data from various existing systems across your plant and that this data can be compared and considered. Data could include instrument or laboratory data, as well as information from mining, maintenance, environmental or other departments. It should also incorporate budget, cost, forecast data and other financial information, and be able to report directly to enterprise reporting systems.
2. Validating and organising data using machine learning
Once you have centralised plant-wide source data, you can then set about validating and organising this data.
Ideally, your solution should use machine learning to support the analysis of huge volumes of data. There are usually three points at which this validation and organisation needs to occur to ensure the quality of the data.
i) Extraction and load stage. Your solution should validate source data to determine if there are missing values or samples and that the values are within an expected range.
ii) Pre-processing stage. Prior to conducting a mass balance, your solution should check measured data marked as critical to spot any instability in the values. Data should also be constantly validated and crossed-checked across the mass balancing process to ensure the measured result aligns with the calculated result at that part of the process.
iii) Post-processing stage. Any calculated values should now be checked against the measured values, and any major deviation should be flagged for resolution or as an improvement opportunity.
3. Digital twin calculations
A process digital twin using dynamic simulation is increasingly important to allow mining and minerals professionals to cross-check results against a second comparative dataset that is generated from a dynamic plant mass balance.
It is important to note that the digital twin for minerals processing is not an Excel-based spreadsheet or a statistical data reconciliation algorithm. Neither of these methods account for the chemistry and process dynamics of the minerals process, nor do they use time as a dimension. They also cannot measure intermediate streams or inventory. These methods put boundaries across several nodes of the process; therefore, data is limited, many assumptions are made, and the probability for error is high. The mass balance process is manual using these older techniques and because of this, it is done infrequently – usually once a month.
A process digital twin using dynamic simulation does use time as a dimension. It can measure inventory, track intermediate streams and cross-check measured plant source data for superior process optimisation. There are no boundaries across nodes and no user assumptions made. Large volumes of calculated data and complete end-to-end automation means a plant-wide mass balance can be performed at an hourly level.
4. Data warehouse
Once you have measured and calculated the data, you then need a place to store it. This is the fourth essential component of a quality digital solution for your plant: a high-performance, structured database that’s highly secure and stable, and allows you to access large amounts of pre-aggregated and organised information.
5. Analysis and reporting
Accurate and fast reports are critical for plant stakeholders.
As well as providing configurable advanced data visualisation and analytics, the right tools will break down barriers and allow authorised personnel to have access to user-friendly and readily available data.
The right tools also automate the reporting function, leaving plant metallurgists to focus on more productive and skilled work that they are trained to do. Automation allows them to make fast, timely decisions and to take prompt action where needed.
Case study: How a gold plant used a digital twin-enabled MES to optimise its gold calculations
Carbon-in-leach (CIL) tanks are difficult to sample, therefore difficult to track due to multiple processes occurring at the tanks. These tanks are continually fed with slurry, and absorption of gold into the carbon occurs in the tanks. The carbon is loaded with gold throughout and transported counter-current to the slurry flow. Given the long residence times, it is computationally difficult to calculate gold in different forms for each tank on a frequent basis. Knowing your work-in-progress gold is vital.
Since a minerals processing digital solution has been in place at this plant, the calculation of gold in the CIL tanks is automated, meaning the inventories can be tracked seamlessly. The digital twin performs a mass balance on the CIL tanks in the circuit every minute and incorporates the equipment operational states of the CIL tanks. This means it can be easily determined when loading/absorption and carbon transfer occurs. Up-to-date LIMS grade for the gold in the solids and carbon absorbed phase are also used in the model when performing the mass balance. Up-to-date analysis of the residue, carbon and solution are captured in mass balance so that the deportment of gold is well understood.
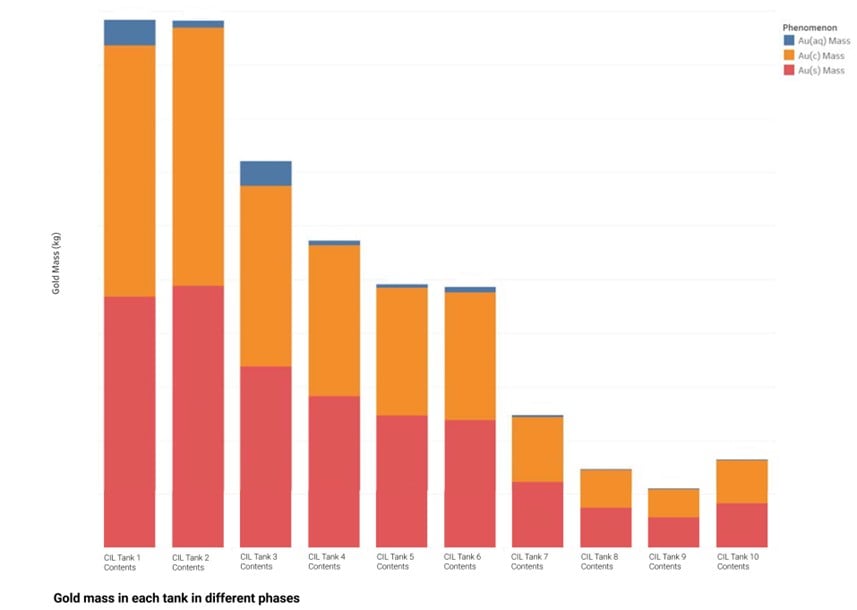
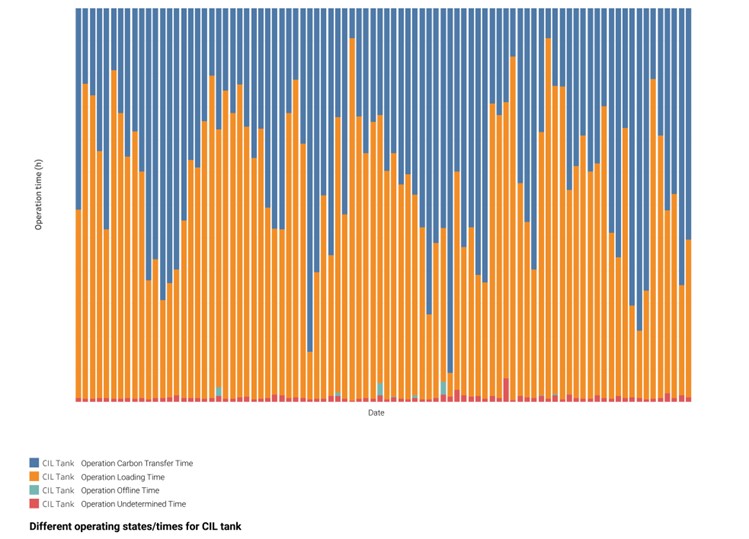
The benefits of focusing on digital transformation for the minerals processing segment
Here are some important benefits of implementing a process digital twin using dynamic simulation specific to minerals processing.
Adherence to compliance standards
Corporate governance is an extremely important consideration. A minerals processing plant can’t have sound corporate governance if there are shortcomings in its plant process information system. A quality digital solution for a minerals processing plant should be Amira P754-compliant. It should adhere to all 10 principles of the code, ensuring data accuracy and transparency. Your solution should also allow you to create an audit trail, meet required stock exchange governance principles, and enable you to quantify, manage and minimise risk.
Sophisticated metallurgical accounting
The main objective of metallurgical accounting is to generate a material/mass balance for your plant. This mass balance is then used to calculate and report process performance and production.
With a sophisticated digital solution in place, a plant should be able to:
- Calculate every stream. You need a complete, up-to-date process flow diagram. All site personnel should be able to rely on this as the most accurate representation of flows within the plant. As the plant operations are updated, so are the dynamic and steady state model flowsheets.
- Automate hourly mass balance measurements. The data from your instrumentation and laboratory data and other data sources should be imported automatically, and an hourly mass balance calculated.
- Save time. Instead of chasing up data to input to the balance software and daily report balance, your metallurgists should have more time to analyse the accuracy and reliability of the data imported and used in their daily balance.
- Track inventory. In a sophisticated customised solution, every stream throughout your plant should be calculated at every hour using real plant data as inputs for the numerous calculations. This should include elemental composition of streams and intermediate inventories.
More reliable and accurate production reporting
Accurate production reporting is used to quantify the performance of processing plants such as recovery and waste. Accurate reporting can also establish an accurate estimate of inventory. If there is a large discrepancy between actual and estimated inventory, there can be significant financial consequences. Poor estimation of recovery and losses can hide process issues and affect production planning.
A sophisticated and purpose-built solution will help a mine achieve zero-based budgeting – where forecasts and budgets require a revised mix of cost and revenue estimates rather than using historical results, plus or minus a few percent. Estimated production and processing costs are therefore based on cost drivers that have been derived from the physical production activities and the physical characteristics of the waste and ore material to be processed at that stage of the life of the mine.
Accurately capturing the mass of concentrate produced is crucial when planning shipments and performing financial activities. Over-estimation of the concentrate stock can result in an over-estimation of the financial value of the concentrate within the plant.
Process optimisation
The ability to optimise your plant’s processes is a fundamental benefit – and is also where your digital transformation project will quickly pay for itself, often before the implementation has even been completed. Process optimisation opportunities using a minerals processing solution can be identified in several ways.
Looking at the alignment between measured and calculated data will allow your metallurgists to detect instruments or sampling practices that may need to be assessed. This means issues can be resolved before they escalate.
For instance, if a plant’s filter conveyor weightometer’s measured value is greater than the calculated value, this either indicates that the weightometer is over-reading, or the flotation matrix is not producing enough of a particular concentrate due to inaccurate inputs. This prompts metallurgists to check the calibration of the weightometer, and check the assays used in the flotation matrix to ensure these samples are representative.
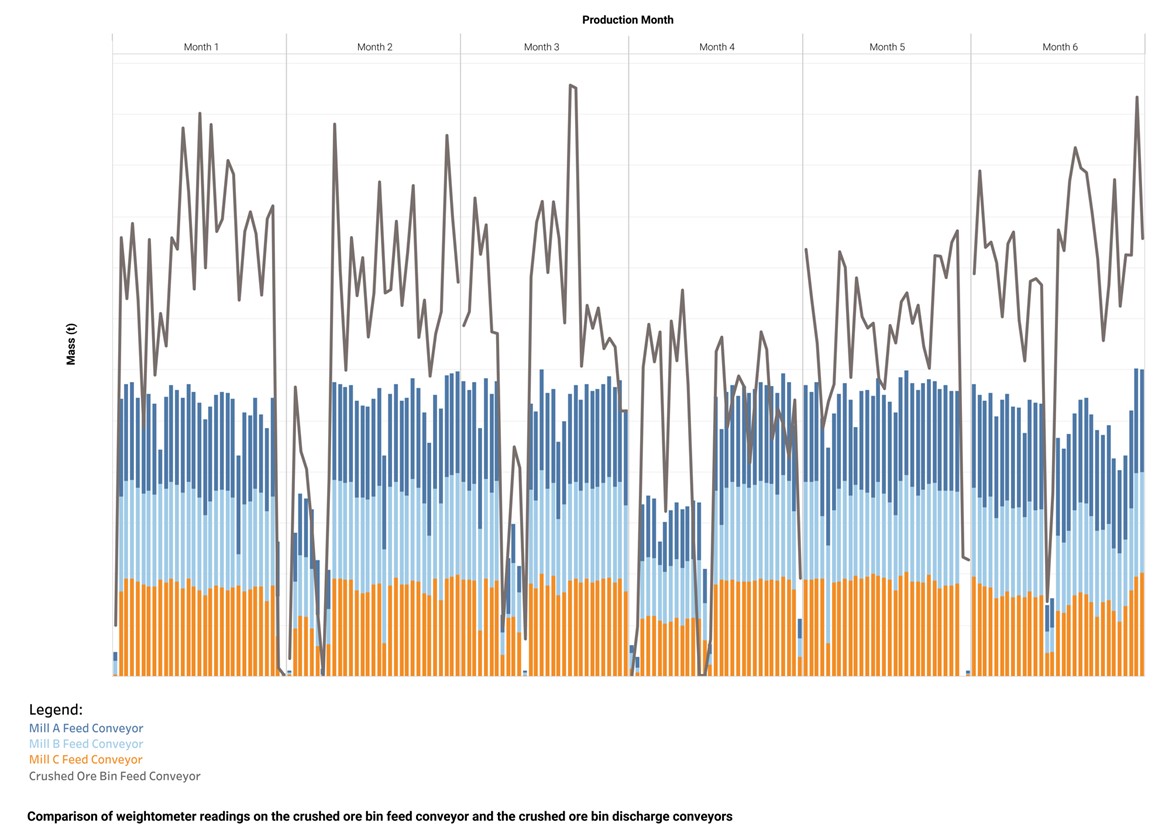
ESG compliance and sustainability reporting
Requirements are moving beyond being loose guidelines to compulsory obligations for individual jurisdictions, and in most countries, reporting on emissions is now mandatory.
Regulators, both in Australia and internationally, welcome the prospect of global standard setting relating to climate and sustainability disclosure. Listed entities are being encouraged to publish these disclosures in their annual reports.
Meeting all these diverse frameworks, standards and requirements is very complex and time consuming. Some require very granular detail, and compliance requirements are also changing frequently.
A purpose-built minerals processing solution can help organisations with their ESG in four key areas: ensuring energy efficiency, yield improvement, reducing greenhouse gas emissions, and driving new, green processes.
When it comes to ESG, a robust MES solution should:
- Provide the organisation with at-a-glance information about their emissions and water consumption, in accordance with reporting standards.
- Enable mining and minerals organisations to test future scenarios. This information can be tied back to financials so organisations can budget and forecast in accordance with ESG principles.
- Track direct process carbon emissions and plant electricity consumption on a daily and hourly basis. This includes consumption of fuels such as coal and diesel, as well as calculated emissions based on plant instrumentation and process chemistry.
- Identify poor performance and optimise performance – resulting in lower overall carbon emissions, and reduced operating costs.
- Be compatible with asset management requirements and for scenario analysis and predictive analytics for process operations.
Find out more
If you missed the first part of this article series, you can find it here. Or read more about digital transformation in minerals processing and Metallurgical Systems’ digital-twin-enabled MES technology here.