Five key levers to improve margins and beat the cost-price squeeze
by Andrew Hall FAusIMM(CP), Director / Executive Lead - Advisory, AMC Consultants
The high metal prices that have prevailed for most of the last decade have triggered a chase for production.
This has compounded the fundamental scarcity in some key inputs, such as experienced and skilled labour, and has been pushing costs up over time. But recently, this has been accelerating, due, in part, to supply chain issues stemming from the COVID-19 pandemic; geopolitical factors, such as war; and, most recently, sky-high inflation. We are now seeing the prices for many minerals, while still relatively high, come off their recent peaks. The combined effect of increased costs and lower prices is squeezing margins.
Five key levers
This certainly isn’t the first time the mining industry has faced similar challenges. What is evident time and again is that the use of blunt instruments, such as cost-cutting and intensive productivity improvement programs, barely scratch the surface. They may deliver some short-term gains, but these are rarely sustained. The big opportunities are typically found by digging a little bit deeper into the key levers of performance to uncover the hidden value by mining smarter.
These opportunities typically don’t require big investment but do require a more sophisticated approach. Five key levers that can drive sustainable performance improvement address both sides of the cash flow equation—that is, costs and revenues. Miners can improve cash margins and reduce business risk by:
- Employing good cost management and control, rather than cost cutting. This will typically result in significant savings that can be sustained. The difference being that a deeper understanding of cost drivers can quickly identify and eliminate wastage and inefficiency without compromising quality or sustainability.
- Getting the most out of the available data. This provides a substantial opportunity to improve productivity and performance. But to do this, it’s essential to set the right KPIs to get data working for you.
- Developing a robust geometallurgical model. This results in more predictable ore and enables higher metallurgical recoveries and reduced cost.
- Reviewing the cut-off grade policy and moving away from break-even grades typically delivers higher cash margins in the short-term and maximizes value over the long-term, thereby de-risking the mine.
- Good mine planning. This ensures that you have a sound and reliable strategy, and are achieving your business goals.
These five key levers are relatively low-cost to implement but will typically drive a significant uplift to the bottom line. And while this is particularly important when margins are under pressure, any time is a good time to initiate them.
1. Cost management and control
There is always temptation to cut costs fast and hard when under margin pressure. While short-term cost reductions are often achieved, they are rarely sustained. This is because most costs are associated with having and maintaining capability and capacity, and typical cost-cutting approaches reduces one, or both, of these critical performance enablers. So-called “lazy” cost-cutting tends to identify and target longer-term activities such as waste development and overburden removal, which aren’t essential to short-term production, but eliminating them will affect the mine’s future ability to achieve its targets.
Consequently, cost-cutting measures are generally not effective and have to be reversed over time. But costs have been increasing alarmingly and something needs to be done. AMC’s SmartData™ shows that, on average, underground mining costs have been rising by over $1.50 per ore tonne per annum above inflation for the past decade. Similarly, open pit costs have been increasing by $1 per tonne mined per annum above inflation in recent years.
The overall impact is that unit mining costs at many mines have doubled in the last five years. While some of the cost increase can be explained by mines getting deeper, the increase is mostly is due to mines paying the price for expanded production to increase metal output, as well as rising input costs, which look likely to continue for a while yet.
More than 25 years of experience in cost estimation and undertaking benchmarking studies at mines all around the world has led to the observation that many mines don’t have a good understanding of their costs. And not enough emphasis is placed on management accounting, with many costs being allocated to high-level cost centres too early within accounting systems. This reduces transparency and understanding and often leads to the type of flawed short-term decisions described earlier. Fixing this isn’t hard, but it needs to be done correctly and requires a thorough understanding of how a mine works.
Understanding costs enables better control. Budgets should be prepared as bottom-up, direct-costed, first-principles estimates. Cost elements are used to build up activity costs, and then the activity costs are integrated with the relevant cost driver to estimate total costs. This needs to be done at a detailed level so the costs are accurate for each activity, for example, different underground development (tunnel) profiles and ground conditions.
Once the budget estimates are accurate, the next step is to ensure the chart of accounts is structured to accurately capture costs at the equipment or functional level before allocations are made to relevant activities. Unfortunately, most accounting systems are set up for financial accounting rather than management accounting so changes to the chart of accounts may be necessary. But even if the chart of accounts can’t be changed, with a little bit of work and mining nous, the costs can be exported at an elemental level and restructured appropriately. This is precisely what AMC does in every benchmarking study undertaken.
Once complete, more accurate budget estimates can be calibrated to actuals and thorough auditing and reconciliation can be undertaken. This enables the quick identification of cost variances and the root cause of wastage and inefficiency. Good cost management and control is a far better approach, both in the short and longer term, rather than the blunt instrument of cost cutting, and it enables wastage and inefficiency to be targeted with precision.
2. Getting the most out of your data
New technologies allow the continuous measurement of operations to ever-increasing levels of accuracy and gather massive amounts of data in real time. But if the data isn’t used to support good decision making and improve what we are doing, then, at best, it becomes a distraction and, at worst, it leads to incorrect and flawed decisions.
When AMC first started benchmarking mines over 25 years ago, the available data was limited, and the quality was often poor. Now nearly all mines have real-time data gathering, providing accurate “live” records of where equipment is and what it is doing, continuously flooding onto the mine’s databases.
But does this lead to a better understanding of how the operation is performing? And does it lead to better performance? Evidence suggests not.
Over the past two decades, AMC’s Smartdata™ shows that the main driver of increased productivity and production has been bigger and more powerful equipment. But equipment operating hours and non-productive time have not materially changed in open pit or underground mines in the past 20 years. In underground mines, on average, the non-productive time for jumbos and long-hole drills is 60 per cent of total calendar hours. For Load-haul-dump machines and trucks, 35 per cent of total calendar hours are non-productive. In open pit mines the average non-productive time for production drills is 30 per cent, while the non-productive time for trucks and loaders is approximately 25 per cent of total calendar hours. So, despite the shift to the “digital mine”, the information is not being used effectively to reduce non-productive time in the mining cycle.
Why? Well, it comes down to having the right KPIs. To effectively monitor mine performance, KPIs need to be holistic and link each activity to the overall performance of the mine. At present, many mines use too many simplistic KPIs that don’t adequately link the different activities in the mining cycle. The data too often becomes the KPI and trying to optimise individual activities in short time increments is driving poor decisions. The result is that non-productive time hasn’t improved.
So what are the right KPIs? The most important is compliance with the plan—but more about that later. The critical KPIs that are often not adequately measured are leading indicators such as ore stocks levels. Maintaining adequate stocks such as drilled, broken, ROM, and exposed ore, as well as the long-term stock levels, such as capital developed stocks, buffer interdependent activities and increase the ability of equipment to work.
High-performing mines consistently and predictably achieve their targets. And they do this by evaluating the performance of the whole mine by focusing on the right leading and lagging KPIs and understanding the links between the different activities that will enable them to reduce variance, be more productive, and achieve their targets.
Using the right KPIs shifts focus onto doing the right things to deliver the desired overall performance. This in turn enables an operating environment that supports high performance. Data and metrics are useful, but they must be used to inform the right KPIs and not become KPIs themselves.
3. Geometallurgy
Everything that happens in a mine depends on the orebody. And yet, many mines still lack a deep understanding about the mineralisation prior to extraction. By leveraging the right data, orebody knowledge can be used to improve everything from grade control to metal production.
Predictive geometallurgy is a proven process that leverages geology, mining, metallurgy, data science and machine learning to produce a 3D block model of the orebody that captures the response of ore to mineral processing. While the natural variability of the orebody can’t be changed, geometallurgy enables the most thorough understanding of the orebody. This is low-hanging fruit, as most operating mines already collect the data needed to better understand and manage this critical issue. In doing so, they gain practical insights into orebody variability to increase recoveries, reduce operating costs, improve stability through more reliable mine planning, and ultimately improve cash flow.
Simplistically, orebody uncertainty in a mining operation costs money in two ways. Firstly, it leads to incorrect decisions, from short-term tactical decisions to long-term strategy. For example, consider a truck load of ore. If the estimated characteristics of the ore are exactly the same as the actual characteristics, the correct decision about where to send the truck is made every time. But uncertainty in the estimates means predicted and actual are rarely identical, so even in a “digital mine”, many trucks are sent to the wrong destination. This means that ore that should go to the heap leach is sent to flotation or to the waste dump. The losses are not recoverable.
Secondly, uncertainty in the orebody leads to mismatches between plant operating settings and the characteristics of the ore feed. Correct settings continuously lag the presentation of the ore. Again, the losses are not recoverable. Inadequate geometallurgy is increasing cost and reducing metal production at mines every hour.
AMC SmartData™ indicates that nearly two-thirds of mines fail to achieve budgeted metallurgical recoveries, and that those that underperform typically do so by 2 to 3 per cent. Just achieving budget targets by uplifting recoveries significantly improves the bottom line.
4. Cut-off grade and strategy optimisation
AMC Hill-of-Value® (HoV) strategy optimisation work conducted over the past 20 years has shown that by changing their cut-off grade strategy, mines can typically improve cash margins and overall project NPV by 30%. Sounds too good to be true? But the evidence doesn’t lie. So why aren’t more mines looking at strategy optimization? The simple reason is that break-even grades are so entrenched in the industry that there is great resistance to think differently. Nearly every mining course, and most of the textbooks we read, present a break-even formula as the way to calculate cut-off grade. A simple break-even formula is shown in Figure 1.
Figure 1.Simple break-even formula.
So what’s wrong with a break-even cut-off? Break-evens are based on the economic theory that when marginal revenue and the marginal cost of production are equal, profit is maximised at that level of output. The problem is, for a typical mine, there are simply too many dependent variables that are linked to the cut-off grade, and the other key inputs can be highly variable.
A simple example in an underground mine is how cut-off grade influences the mining shapes, which in turn impacts the mineable inventory and production rate, which affects the operating and capital costs. So, when you change your cut-off, you also change your production rate and costs. Over the last five years, mines have experienced wide variations in prices, exchange rates and input costs. And when you combine this cost-price variability with the inherent variability in orebodies discussed earlier, it is clear that all the inputs to the equation are either highly variable, are out of our control, or are dependent. These are factors miners have no control over. The inescapable conclusion is that break-even is broken!
So what’s the answer? Understanding that you can’t calculate an optimal cut-off grade is the first step. And once that realisation is made, a whole range of opportunities open up. Without getting into all the theory, optimal cut-off grade is more related to capacity and the grade distribution of the mineralisation than it is to metal prices or costs. And that’s good news because we typically can’t control prices and we have limited control over costs, but we can control what we mine and at what capacity.
Determining the optimal cut-off grade requires the development of value curves for each different option. The example in Figure 2 shows a HoV evaluation for an actual open pit mine. NPV is charted on the vertical axis, and ore processing rate and total rock mining rate on the horizontal axis, at a constant cut-off grade. For this operating mine increasing the processing rate by 30% and doubling the mining rate, will substantially increase NPV and cashflow, at the particular price assumption used.
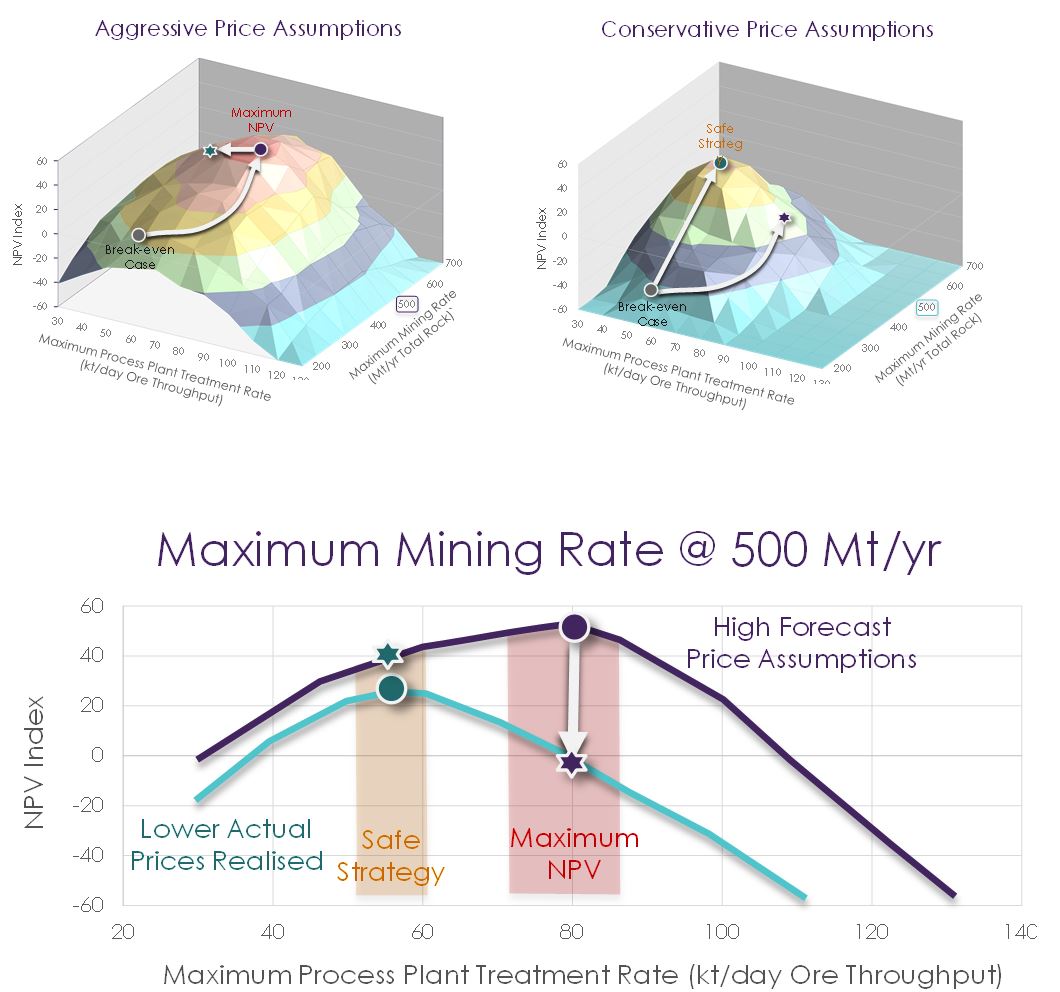
Figure 2. Typical HoV evaluation for an open pit mine
But understanding the shape of the curves is much more important than where the peak of the hill is. If we review the same options at a lower price scenario, the shape of the hill changes dramatically and the position of the peak shifts. If we selected the options that maximised NPV at more aggressive prices it barely makes money. But if we selected the safe option, that is the option that maximizes NPV at conservative prices, we still make good margins at the lower price, and we realise nearly all of the upside during higher prices. The HoV approach not only helps to maximize margins, but it enables the selection of a strategy that de-risks the mine.
HoV saves time and money by reducing the manual mine planning effort, and, because all the potential options are considered and evaluated for all scenarios, there is no rework or further investigation required at the back-end of the study.
Getting the cut-off grade policy right is a significant lever in improving margins throughout the price cycle and de-risking the mine over the long-term.
5. Mine planning
Good performance is about achieving a plan that delivers the corporate strategy day-in and day-out.
Mine planning, when functioning well, pulls everything together. Strategy optimisation can provide the right strategic direction, but good mine planning materialises this in practice through practical and achievable mine plans that identify operational risks so they can be effectively managed, and opportunities for improvement incorporated. The mine plan should be broken down to the appropriate level, where activities can be executed by operations and aligned with all key stakeholders. And finally, good mine planning involves routine reconciliation and monitoring of compliance to ensure the operations stays on track.
The most strategically important KPI is spatial compliance to plan, as nothing adds more value than close alignment between strategy and operations. But the opposite is also true. The biggest risk to most mines is misalignment between strategic intent and what is happening at the face. Unfortunately, this is all too common, often driven by simplistic analysis and the wrong KPIs.
Good mine planning is essential to high performance as it balances the needs of ensuring future targets can be achieved with delivering on targets today. For example, we typically see significantly more excavator moves in open pit mines than planned moves due to a lack of orebody knowledge and grade control issues. Greater priority is placed on chasing metal, and the plan is ignored. This type of short-term thinking results in increased non-productive time and lost production that can never be recovered. A similar example in underground mining is congestion being a major impediment to productivity. The root cause is often a lack of timely waste development resulting in a smaller number of working areas and too many activities happening in one place at one time creating a bottleneck to production.
Simply preparing and adhering to a good mine plan addresses most of the common operational issues and inefficiencies and facilitates high performance. So, making sure that mine planning is functioning well should be a priority for all mines.
Concluding remarks
In conclusion we, as an industry, are facing challenges and uncertainty. This is nothing new and could last for some time. But there is significant opportunity to improve margins by repositioning operations and mining smarter. We need to make sure we focus on what really matters.
Five key levers that provide significant opportunities to sustainably improve margins are to avoid cost cutting and focus on cost management and control; set the right KPIs and get more out of the available production data; understand the orebody better through predictive geometallurgy; undertake strategy optimisation and review the cut-off grade strategy (break-even is broken!); and get mine planning in order so what’s planned gets done.