Re-imagining the way we work
From product lifecycle management to integrated modeling and simulation
For many car, boat, and aircraft manufacturers, product lifecycle management (PLM) is a fact of life. They have a product they need to manage from the glimmer of an idea through to design, development, manufacturing, sales, and end-of-life. And many have chosen to pursue PLM to help them deliver a high-quality product at as low a cost as possible – and in the fastest possible time to market.
Mining also produces a product, and our mining value chain is in fact not all that different from an SUV, yacht, or plane. However, while I believe we can learn a lot from PLM methods and principles, our industry is clearly not the same as car or plane manufacturing.
We need to take what works from PLM — especially viewing what we do as creating a product, from ideation to end-of-life — and then customise it to suit the complexities of our industry and the lengthy process of moving from mineral discovery to mine decommissioning.
We also need to provide our teams and stakeholders with ways to experience the progress of the mining value chain, to experience the way our product moves over the life of an asset, because that is the fastest and best method for shared understanding and reliable decision making. And the key to that is PLM combined with virtual twin experiences.
A new way to visualise your systems
Many miners view the mining value chain as a linear chain that moves, like a car, from design to assembly line to sales room. But that’s not the way mining actually works, is it? Mining must continually adapt and adjust to nature, and has many more feedback loops than the average car manufacturer, meaning we also end up with less control over the results of our work.
Another potentially more useful way to visualise the mining value chain is as a complex series of interconnected systems. For the chain to work at its best, each system must be able to work easily with, and connect to, the next.
Through virtual twin experiences, you can begin to visualise your systems as a collection of tiered virtual twins, each with its own data sources, processes, and areas of knowledge, like this:
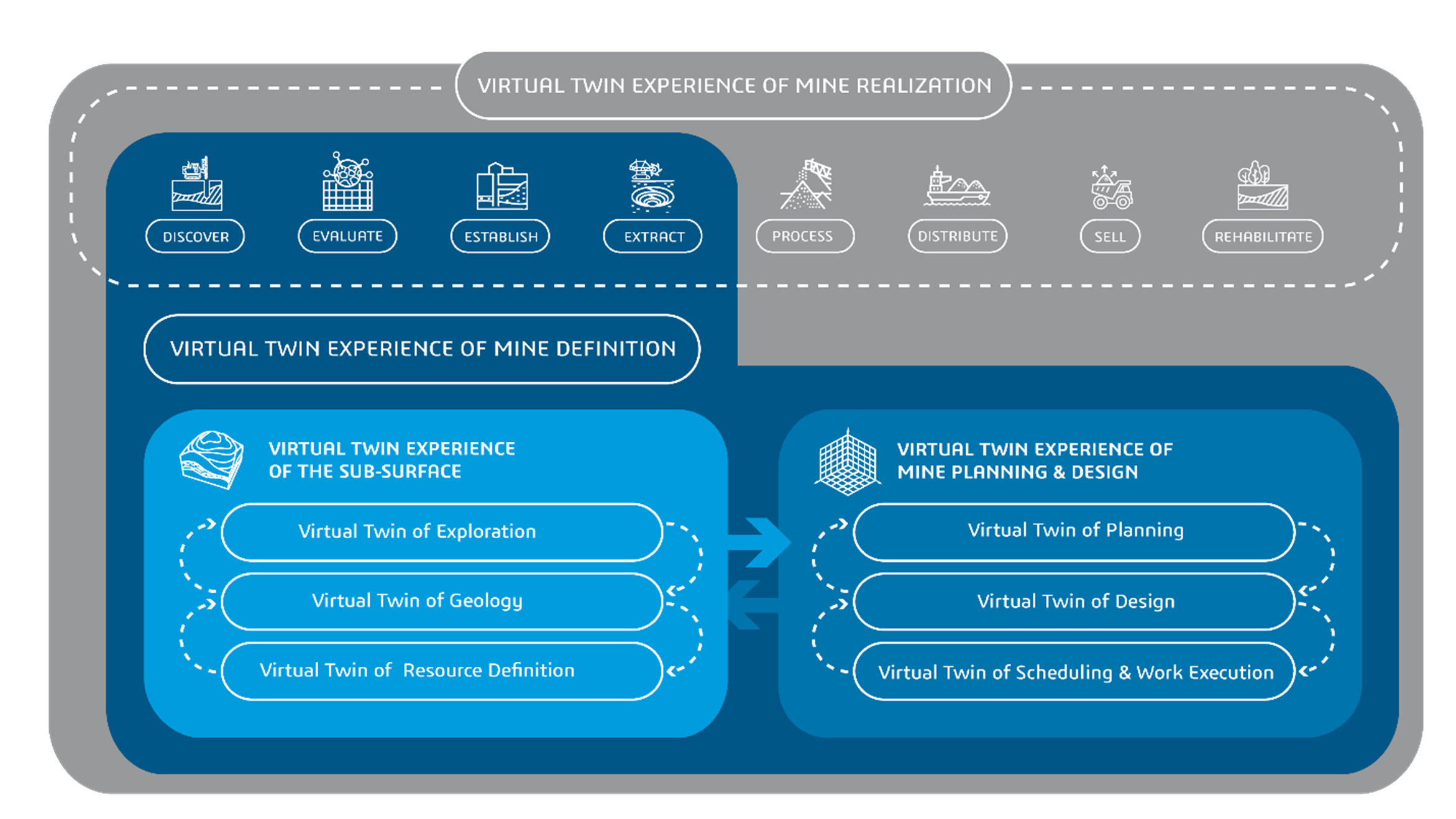
The virtual tiers are linked in a way that enables them to work together to respond to problems that arise along the value chain.
Virtual versus digital twin
A digital twin is the digital prototype of an object — its virtual version. Virtual twin experiences, on the other hand, not only create 3D digital twins, they also allow you to model, visualise, and simulate entire processes and systems, and to add in real-world data and feedback to continually inform and improve your data.
For example, a car manufacturer might use virtual twin experiences across the product lifecycle to:
- generate a design
- simulate how that design would hold up in various situations, such as braking in heavy snow
- visualise and compare how different suppliers would affect the supply chain and the overall carbon emission levels of the finished product
- analyse data coming in from a process or the product in its real-world usage, run additional tests, and make changes to ensure continuous improvement and prevent unexpected downtime
- determine how various materials in the vehicle can be recovered and reused at end of life.
Virtual twin experiences can work just as well for miners, provided you first consolidate your data.
Consolidating your data
In the mining industry, data comes in many formats and from many different data sources, often with unique data models. If you can consolidate all your data into one central location and then give that data a common language, you ensure that all your data can be employed to contribute to your knowledge base.
One of the most efficient ways to do this is to work with a software package that can help you both:
- use a semantic data model to consolidate your data, where structured or unstructured data existing in any source is organised to add meaning by creating data relationships between the data sources and to allow the same information to be viewed in multiple ways, without human intervention or additional processing
- adopt industry standards and dictionaries to ensure one data source will always speak to another data source.
Benefits
Once your data is consolidated and using a common language, you will now be able to take full advantage of working within a virtual twin. The benefits include being able to:
Easily control and manage your data
A virtual twin makes it easy to control and manage your data across teams to ensure the data is synchronised and that the right people have the right access at the right time to the latest version.
Use case
Say your mine completed a summer drilling campaign to improve your resource definition. You have just received the assay sample results from the lab, which means your borehole databases must be updated.
The virtual twin automatically notifies your exploration geologist that the approved geology logs and assay results are now available, and the geologist, who is authorised to make changes:
- creates a new iteration of the exploration borehole database with the new data incorporated, without losing any earlier versions of that database
- visually validates the new data, and
- sends a request through an automated approvals chain to approve the boreholes for use in updating the geology model and resource definition.
The geologist’s manager reviews and approves the new database iteration, and the virtual twin automatically:
- notifies your geology modeler that a new version of the borehole database is available
- generates the new geology model based on pre-installed parameters for implicit geology modeling — allowing your geology modeler to focus on analysing the results rather than performing manual updates.
After the geology modeler refines the new geology model and the manager again reviews and approves it, the twin sends it on to the resource modeler who updates the resource definition.
Use parametric modeling to run virtual scenarios
Parametric modeling is key to taking your cleaned and consolidated data and using it to run comprehensive virtual scenarios — not just within each tier but between all your tiered virtual twins — to stress-test designs and engineering principles.
Traditional CAD-based design works well but, because it requires a designer to modify the entire shape of a design in response to a change, it is slow.
Parametric modeling removes or significantly reduces the amount of manual digitisation a designer is required to do and adds the power of associativity, which preserves the link between reference data — such as terrains and geology or resource models — and existing infrastructure models, making it possible to update designs automatically every time there is new input data.
Use case
Your mine designer has generated several optimal stope shapes for an underground mine and now needs to evaluate different access designs and mining methods to deplete these stopes.
Using a parametric design tool, the designer associates:
- the stopes to the target access design to rapidly re-evaluate the design to be modeled should the stopes be modified
- each tunnel and access design into a network that can propagate changes should the dimensions or location of a preceding tunnel be changed.
Then the designer:
- builds a library of templates for each part of the development network, such as drifts, ramps, accesses, or raises, as well as the geometrical parameters associated with each, including profile, slope, spacing, and size
- tests the templates — for example, by varying tunnel heights, altering the radius of a ramp, or changing a gradient — to ensure they are working
- establishes rules and logic that will enable the templates to both automatically update the entire design and ensure the end-product is operationally feasible
- defines safety and operational principles to ensure a robust and practical design can be achieved
- tests and validates the performance of the parametric design.
Add generative design and MODSIM to analyse options
Mines today face many constraints when designing a new mine — geotechnical, environmental, financial, regulatory, etc. To ensure the best possible mine design, designers need to be able to evaluate thousands of configurations against possibly hundreds of constraints in order to find the one design that offers the best trade-off.
Generative design, a form of artificial intelligence, is an iterative design process where designers tell the software what the limits and the possibilities are for the constraints they have identified.
Many of today’s foremost manufacturers use generative design to improve product performance, reduce costs, and increase sustainability. However, while generative design will help eliminate a range of possible designs, it will not by itself help a manufacturer be absolutely confident it is making the right design choice. The manufacturer also needs to test its final choices in the most rigourous way possible, through modeling and real-life scenarios and simulations.
In mining, the traditional approach is for design/modeling and simulation to be done by different teams with different schedules and priorities, which often results in simulation and simulation analysis starting at the very end of the design process.
Integrated modeling and simulation — or MODSIM — allows geoscientists, engineers, and analysts to work together from the beginning of a mine project, opening up opportunities for teams to explore many more design alternatives in less time and with less friction (no having to translate data from system to system and avoiding the risk of file-sharing errors). It also ensures faster review cycles and, ultimately, a better, more reliable mine design.
Use case
A mine company is doing a feasibility study for a new mining operation. Like all mines today, it wants to maximise revenue early to reduce the impact of capital investment, and to design an efficient mine capable of offering a steady rate of extraction over the long term.
The design/planning team knows their design must consider the size of the mine, the number of phases, phase starting points, and direction of phases. They also understand that both variables they cannot control, such as price and cost fluctuations and inconsistencies in ore grade, and variables they can control, like fleet dimensioning, sequencing alternatives, and scales of construction, will influence each decision.
Using generative design and MODSIM together, the team evaluates, within a matter of hours, various planning and design implications through a one-stop planning and design process:
The team first generates 23 pit options analysed from eight different directions, then 1,600 alternatives for the 23 pits based on the NPV obtained for each possible pushback direction plus the target KPIs that most affect their decision making.
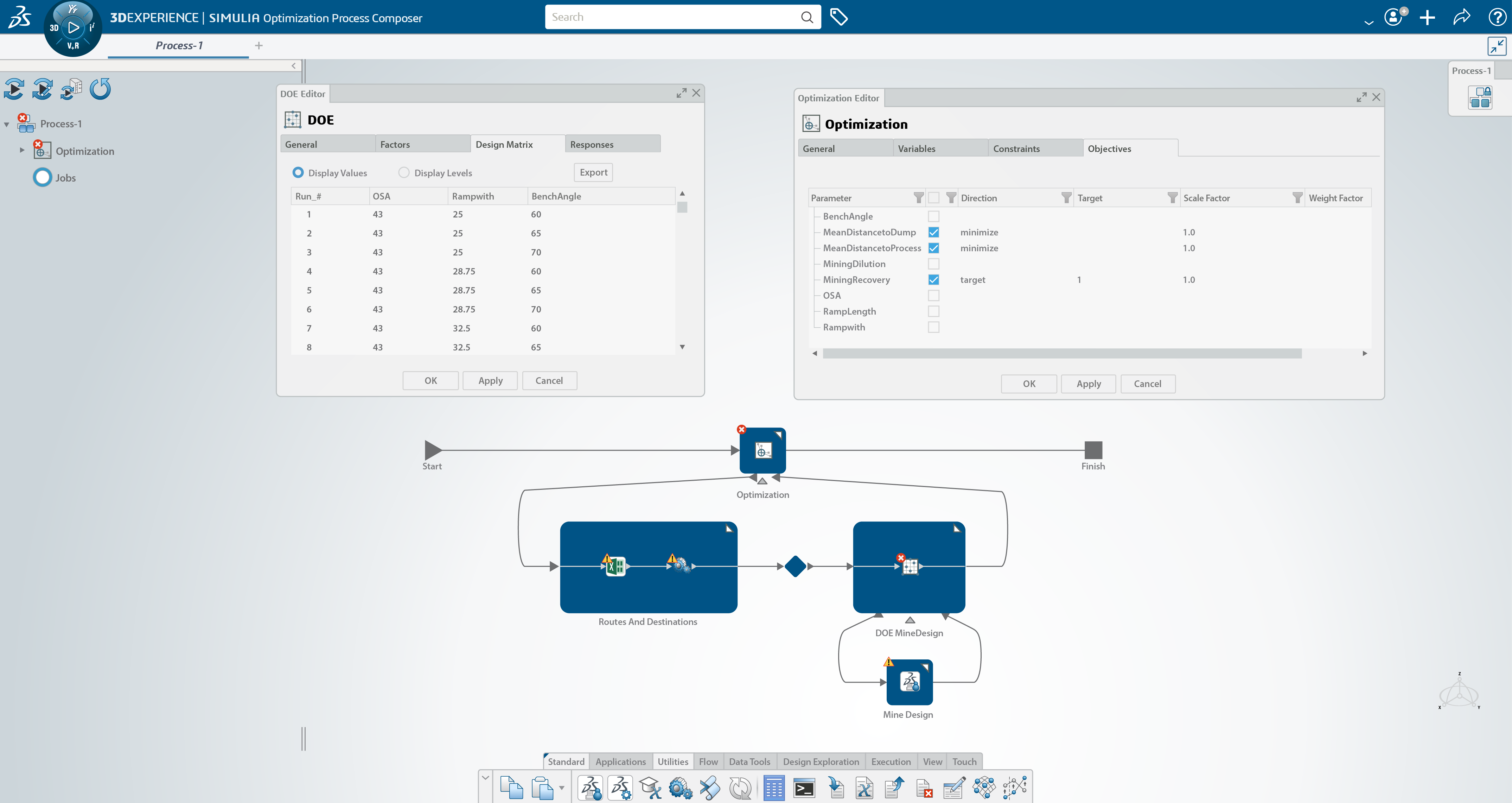
- After whittling down the options to the one with the best pushback dimensions for extracting maximum ore, the team:
- develops a production plan that considers such factors as mining rate, CAPEX impacts, location of waste facilities and haulage logistics
- generates 9,680 possible sequences (and the hill of value visual, below) with different cut-off grades, prices, production capabilities, and corresponding CAPEX.
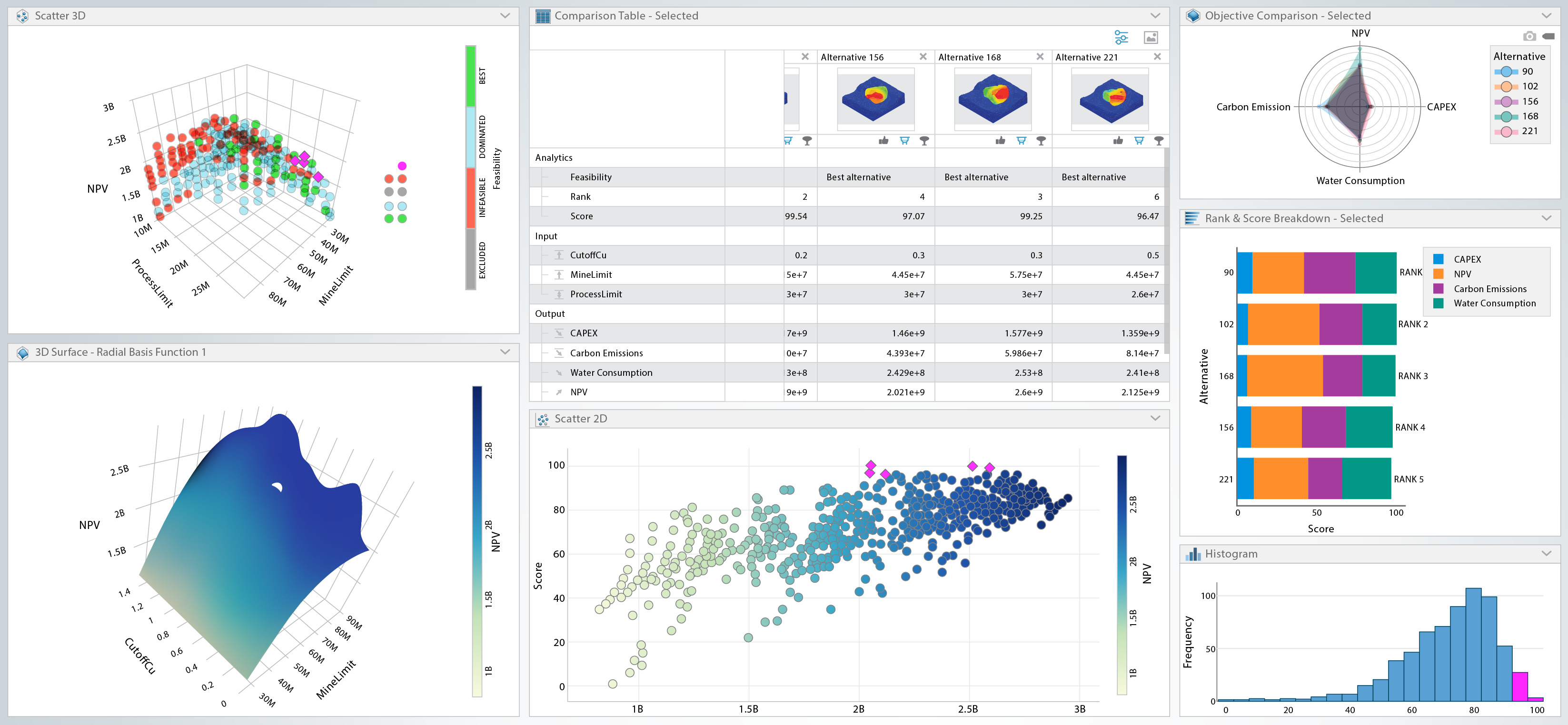
- From there, each of the possible plans automatically generates its own NPV, with its own hill of value visual, making it easy for the team to see which plan creates the optimal production range.
- This is good, but the team wants even more precision, so they now use parametric design to identify optimal and practical trade-offs that will ensure their final design plan meets all critical geotechnical and safety rules.
A different way to work
Data consolidation, combined with virtual twin experiences, parametric modeling, generative design, and MODSIM, enables mines to generate multiple new perspectives into what has happened, is happening, or will happen, at a mine site. And with more perspectives comes a greater chance of making the best possible choices that will lead to the best possible results.
It’s a different way to work. It takes a little imagination and no small leap of faith. But the technology is here, it works, and it’s time for the world of mining to catch up with what other product manufacturers have been doing for years.