Slurry pump selection – Choosing the right solution for your duty
When looking at a new pump installation, it is all about the data. In an ideal world we would have one pump for all duties, making life easy for suppliers and operators alike. Unfortunately, life is rarely this easy, hence why there are many types of pumps. Read on in this article as we discuss about selection criteria and considerations when selecting the optimal pump for your operation.
As a minimum, it is normally required to have both the flow and head of the duty. This will allow for a very basic selection using the available pump curves. It is worth keeping in mind that published curves from manufacturers are based on clean water. This is due to the many various slurries that are available, which would require manufacturers to supply thousands of curves and would not be feasible. This is where manufacturer pump sizing tools come in handy, such as the Metso Outotec PumpDim™ tool, which takes the supplied slurry data and system information to provide an adjusted ‘slurry curve’. This results in the tool providing an optimal pump recommendation for the operation.
However, no matter how good a calculation tool is, the result is dependent on the data that is provided. The saying, “Rubbish in means rubbish out," is very relevant here. Depending on the abrasiveness of the application, pumps have a sweet spot in which they like to work.
This is called the preferred operating range, which is a percentage of the best efficiency point (BEP). The more abrasive the application, the smaller this sweet spot becomes. To simplify things, these ranges are organized into service classes as determined by the Hydraulics Institute and uses the average particle size (d50) and the slurry specific gravity. Starting at Service Class 1, which is essentially a water duty, and making its way up to the very highly abrasive Service Class 4, which would be like a Mill Discharge application. Using these service classes, we can determine the correct pump to be used along with ensuring the speed of the pump is also correct.
The duty/service class is also used to provide recommended limits for other calculations such as stage pumping and impeller tip speeds.
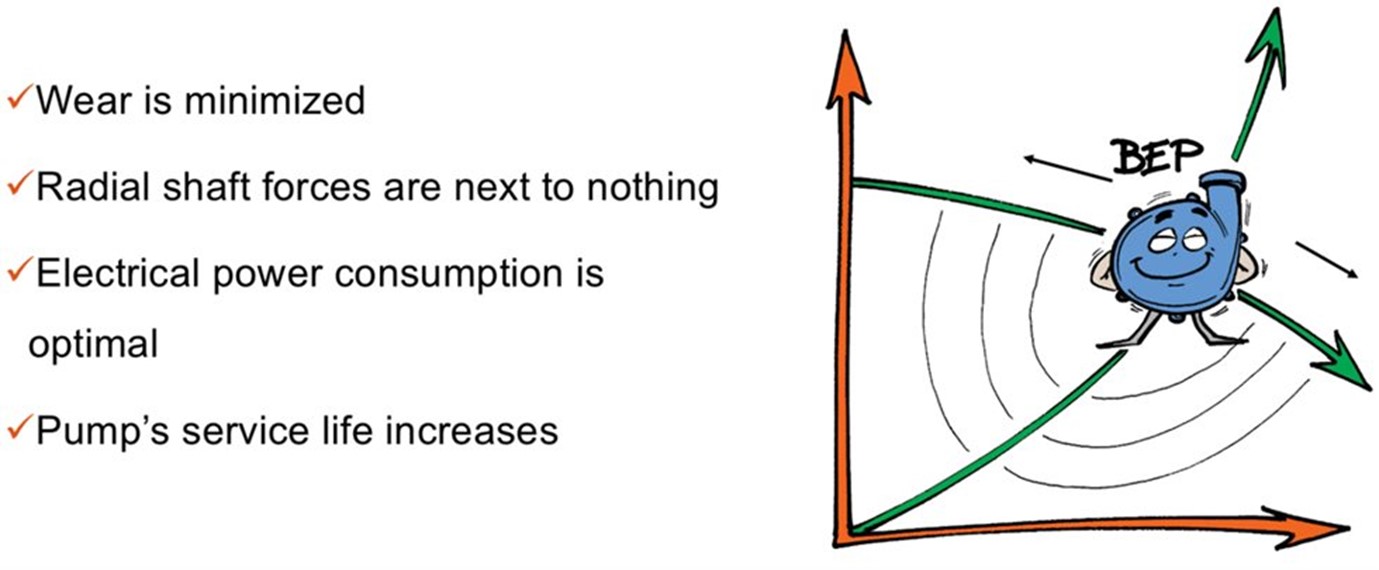
The importance of data
The importance of data can easily be overlooked especially with a pump that is already installed and has been running on its calculated duty point for some time. As sites develop, it is normal for duty points to change as manufacturing fluctuates to the market demand. An increase in flow may not be considered a major factor on some equipment, but when it comes to a pump it can push its operation from the most efficient point toward a critical range. There are other factors that can have detrimental impacts such as changes in the feed material and installation alterations to pipework like lengths, dimensions, and others. This can result in an increase in friction losses in the system.
The reason pumps like to work at its most efficient point is because this reduces the amount of wear seen, ultimately extending the service life. It is well known in the industry that slurry pumps will not be able to run forever due to the nature of its work. But every mine aims to extend this life as much as possible, which happens by being as close to BEP as possible.
Small adjustments in flow or head can move the duty point on the curve considerably has and have implications on wear life. Moving further to the left of BEP, usually due to a reduction of flow or head, creating recirculation in the pump meaning the material travels around the casing excessively before it is moved down the line. This creates additional wear due to the extra circulation of particles.
Alternatively, the duty point can be pushed to the right of BEP by increasing the flow. This can cause issues with inlet velocity meaning the flow into the pump is greater than the installed size that the pump can manage. And resulting in increased wear rate around the discharge area of the casing and on the eye of the impeller, which is the first obstruction the flow finds when entering the pump.
In some of these cases a pump can be adjusted on speed to help deal with the changes of duty, but in other cases it would be recommended to change the pump size to best fit the altered application. Without taking these changes into consideration, a previously well performing pump can turn into a maintenance headache.
Another factor to keep in mind is that as a pump wears and moves away from its optimum point it has a reflective effect on the power consumption. An increase in power consumption turns into an increase in costs and carbon footprint.
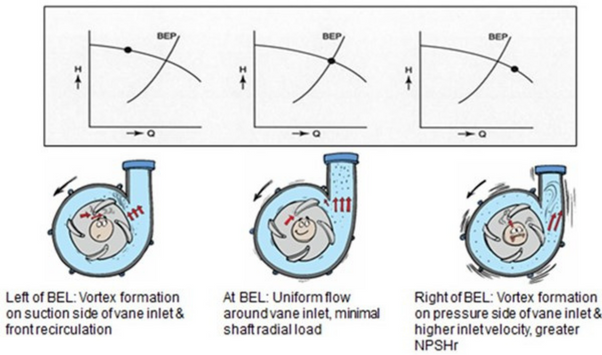
When in doubt, get it checked!
The best action to take is to reach out to your pump supplier when considering any change in duty details. They will be able to check the suitability of the equipment, which is in place and make recommendations as to any actions or alterations that may need to be made to ensure a smooth transition when updating site processes.
More information
Access more information on PumpDim (slurry pump selection tool) here, and a free slurry pump e-handbook here.
A version of this article was originally published at mogroup.com and is published here with Metso Outotec’s permission.