Technology to help miners meet sustainability goals
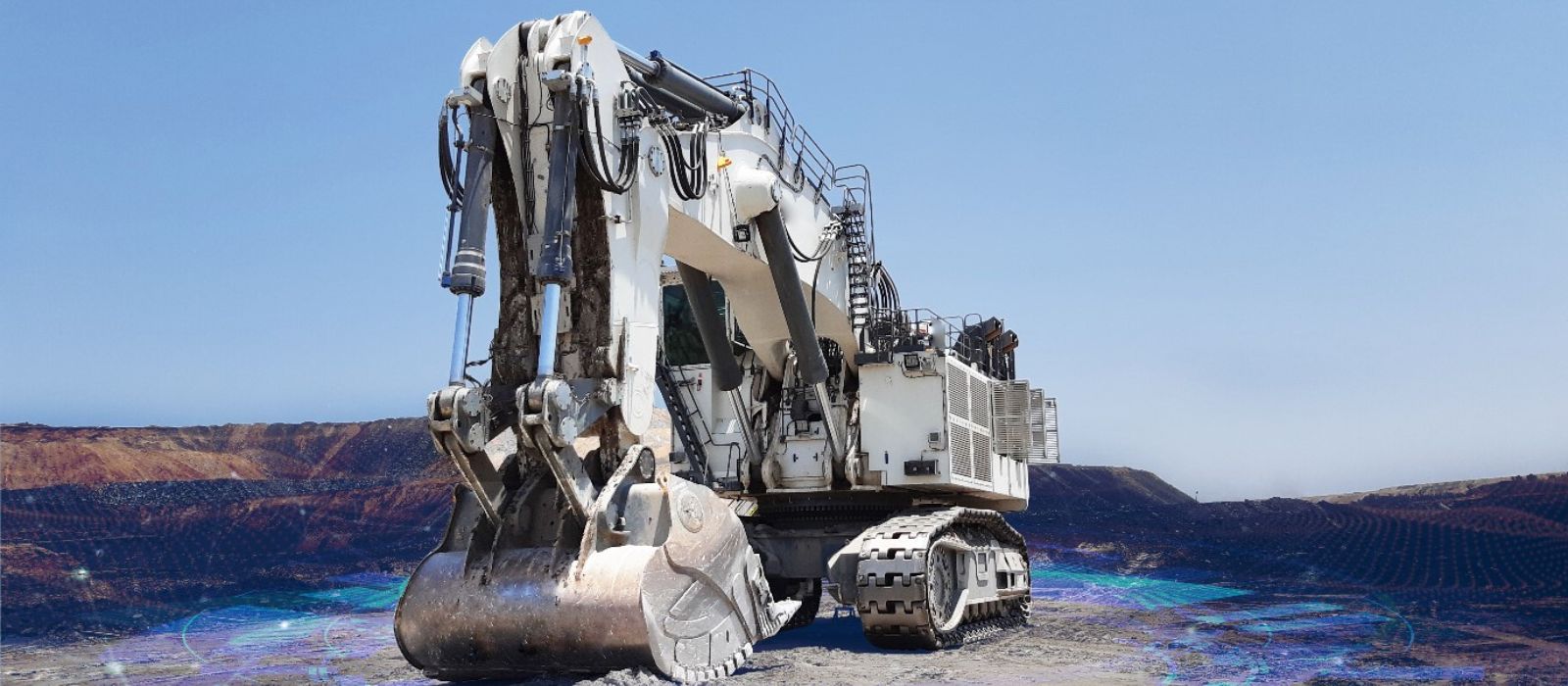
Governments, investors, and employees are demanding that corporations take action on environmental issues, and the mining industry is no exception.
There's no single solution to these complex challenges, but technology presents significant opportunities to make progress on sustainability goals.
Reducing greenhouse gas emissions in mining
Miners worldwide are increasingly focused on greenhouse gas (GHG) emissions reduction. The extraction and primary processing of minerals are a significant cause of carbon emissions (26 per cent of global totals – including scope 3 emissions – according to Global Data).
Energy consumption and intensity in mining and mineral processing are rising at around six per cent each year, largely due to the declining grade of ore bodies and the increasing amount of waste that must be removed to access them (Deloitte, 2016).
And yet, critical minerals like lithium and cobalt are essential for an electrified future.
While innovations like electrification and green hydrogen will significantly cut emissions, many of these technologies are prohibitively expensive or still in development.
Miners need to take steps to optimise their mining value chain with technology that exists today.
One obvious target: reducing the amount of diesel burned in mobile equipment. According to McKinsey, approximately 40-50 per cent of a mine's CO2 equivalent (CO2e) emissions come from diesel used in mobile equipment (Legge et al, 2021).
But there are smart solutions that can help miners reduce energy requirements at multiple points in the value chain while also improving productivity.
Optimised drill and blast
There are three significant opportunities to reduce emissions from drilling and blasting: drilling to pattern, drilling to target depth, and using rock hardness to minimise explosives.
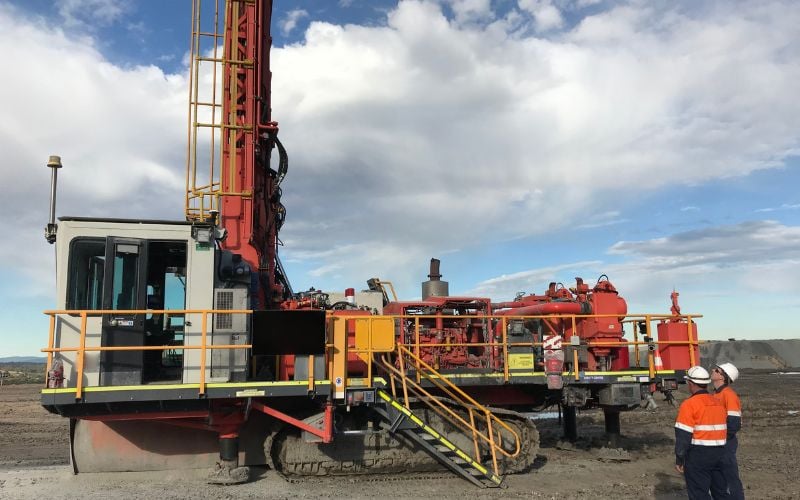
For example, CR Mining has developed a high-precision GPS navigation system for rotary blast drills, called Thunderbird 1110TM. By providing in-cab guidance, this enables operators to navigate directly to the next hole location, which minimises fuel use, and drill accurately to plan.
When holes aren't drilled to plan, more explosives must be used, or rock ends up poorly fragmented. Both result in increased emissions, either from additional explosives or increased dig energy required to move poorly fragmented rock.
Thunderbird also provides drill depth guidance. By avoiding over-drilling, drills waste less fuel, further reducing emission intensity. Eliminating drill depth errors and associated drill time can save significant amounts of CO2e emissions per drill annually.
Furthermore, by understanding rock composition so only the necessary explosives are used, emissions can be further minimised. For example, technology can now generate maps of rock hardness, helping operations blast accurately and reducing wasted explosives.
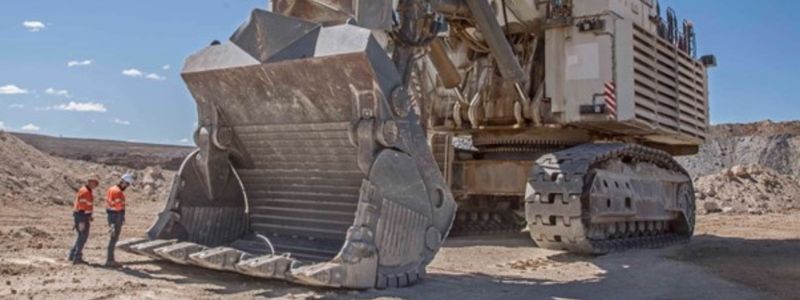
Reducing dig energy for excavators
By digging more efficiently, data collected on site shows that excavators can burn less fuel, reducing CO2e emissions by up to 38 kg CO2e/hr, adding up to a savings of 217 tonnes of CO2e annually, depending on mining conditions.
In response to this, CR Mining has developed a cast lip (called Stingray) for large hydraulic excavators, which is designed to improve digging performance and reduce dig energy. Casting the lip in a single piece allows a reduction in weight without impacting strength. The lip profile also allows material to flow with less resistance, so buckets can penetrate dirt with less effort. This translates to a dig energy reduction of up to 13 per cent compared to alternative lip systems.
Opportunities in the load haul circuit
Despite technological advances, load haul circuits remain wasteful and highly variable. In an analysis of one Australian iron ore mine, McKinsey estimated that 45-52 per cent of total emissions were associated with loading and hauling (Legge et al, 2021).
Research published in the International Journal of Mining Science and Technology found that reducing payload standard deviation from 30 per cent to zero can save up to 35 per cent of total fuel costs and CO2e emissions (Soofastaei et al, 2015). Payload standard deviation measures the variation between the lowest truck payload and the highest; lower standard deviation indicates that trucks are being loaded more consistently to target payload.
By optimising the load and haul circuit so that the majority of trucks are loaded to target payload (eg with a tighter payload distribution), trucks will make fewer trips while making the most efficient use of fuel, reducing CO2e emissions per tonne of dirt.
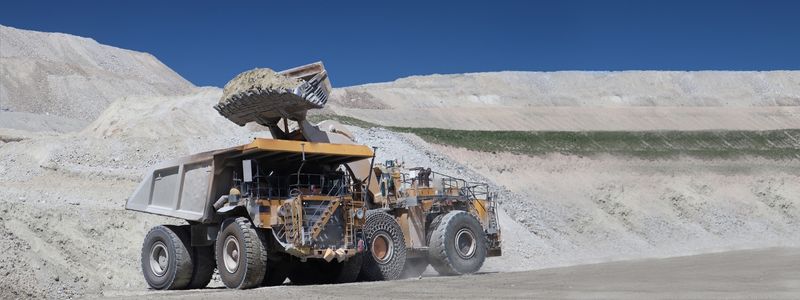
An excavator and loader-based payload management system, such as CR Mining’s Titan 3330 TM, can help address this issue by measuring real-time bucket payload and total truck progress to target. More accurate than truck-based systems, operators get real-time feedback so they can make immediate adjustments to load trucks more precisely. This technology can reduce payload variability, tighten spreads, and increase average truck payloads without increasing overloads, meaning more tonnes per equivalent emission footprint.
In a recent case study in collaboration with CR Mining, one iron ore miner increased median truck fleet payload from 227 to 239 tonnes, adding up to over 10 million additional tonnes moved by the same fleet in a year.
Through increased average truck payload, the miner decreased litres of diesel burned per tonne by 0.8 per cent, equivalent to saving ~1.3 million litres over 800,000+ truck loads in a year. This equates to savings of 3,500 tonnes of CO2e emissions.
Implementing excavator and loader-based payload management systems and increasing average payloads while tightening spreads is something miners can do today to reduce emission intensity on the road to achieving sustainability goals.
Find out more
If you’d like to learn more, you can get more information on the technology discussed in this article at the CR Mining website.
References
Deloitte, 2016. ‘The bottom line: Driving value through energy management in mining’ [online]. Available from: https://www2.deloitte.com/content/dam/Deloitte/au/Documents/energy-resources/deloitte-au-er-driving-value-through-mining-231116.pdf
Legge H, Muller-Falcke C, Naucler T and Ostgren E, 2021. ‘Creating the zero carbon mine’, McKinsey & Company [online]. Available from: https://www.mckinsey.com/industries/metals-and-mining/our-insights/creating-the-zero-carbon-mine
Soofastaei A, Aminossadati S, Knights P and Kizil M S, 2015. ‘A Comprehensive Investigation of Loading Variance Influence on Fuel Consumption and Gas Emissions in Mine Haulage Operation’, International Journal of Mining Science and Technology 26(6). Available from: https://www.researchgate.net/publication/295387170_A_Comprehensive_Investigation_of_Loading_Variance_Influence_on_Fuel_Consumption_and_Gas_Emissions_in_Mine_Haulage_Operation