Up for the challenge – delivering the Mina Justa Project
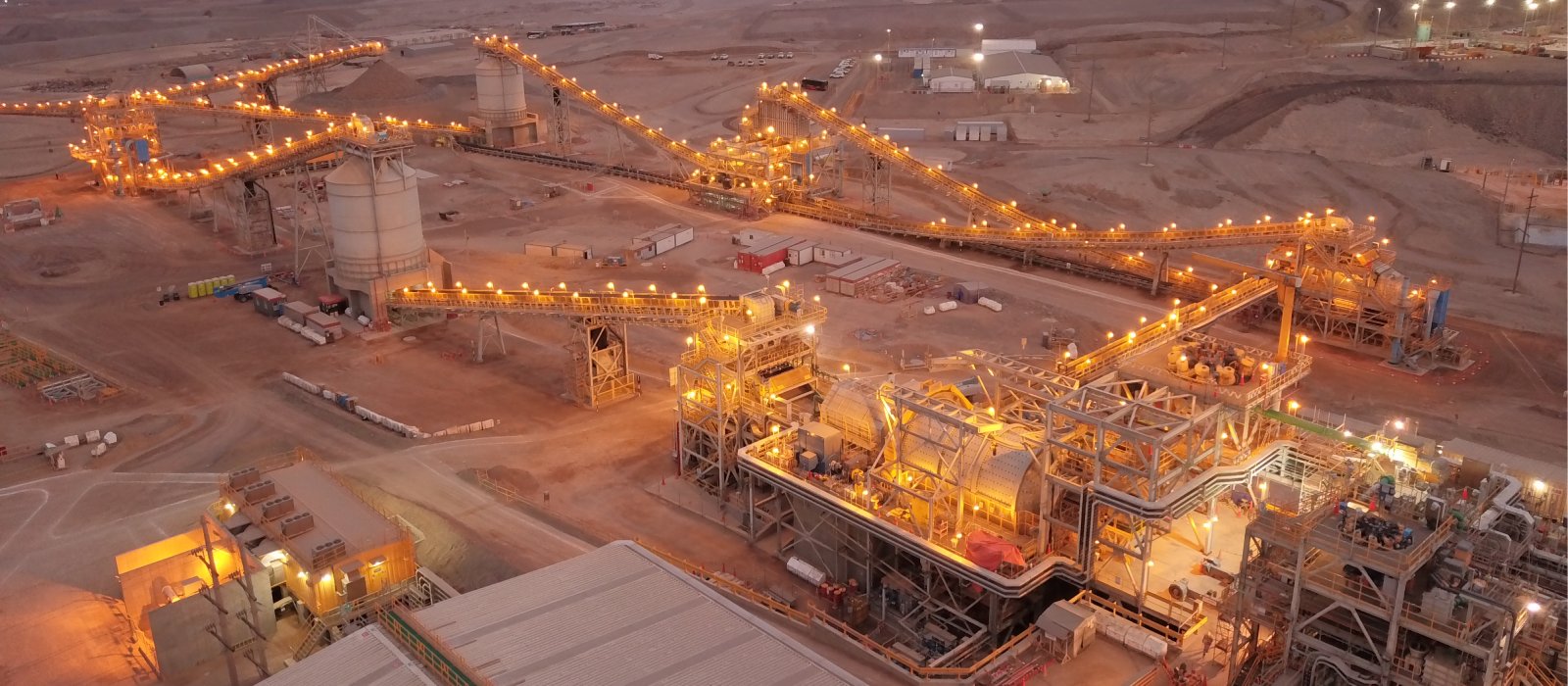
This article is based on the original publication 'Mina Justa, un Proyecto retador', in Energiminas Magazine, and is published with permission. Project updates from 2021 have been added.
The Mina Justa Project, owned by Marcobre S.A.C., is located in the Ica Province of Peru. The Project consists of two open pit mines and two processing facilities, with a projected annual production of ~100,000 tons of copper contained in cathodes and concentrates.
When reflecting on the most challenging aspects of delivering this EPCM project to-date, I believe these were the complexity of the process plants and managing the impacts of COVID-19; the pandemic being the greatest one without a doubt.
During the quarantine in Peru, the project was halted to implement the Mina Justa Prevention, Surveillance and Control Plan, ensuring the safety of all employees and contractors. Along with Marcobre, Ausenco implemented COVID-19 protocols and readjusted the schedule to ensure that the project proceeded safely. The project is on-track according to the revised schedule and budget thanks to the incredible support and work of the entire team who put safety at the forefront.
Working alongside Marcobre, Ausenco helped progress the Project from Prefeasibility Study through Definition Phase Study, Independent Peer Review and into the Execution Phase.
With a global reputation for innovative cost-effective, lean design models; extensive experience in EPC and EPCM; and especially the successful delivery of the highly capital efficient Constancia Copper Mine EPCM project, Ausenco were trusted by Marcobre to deliver the best results for the Mina Justa Project.
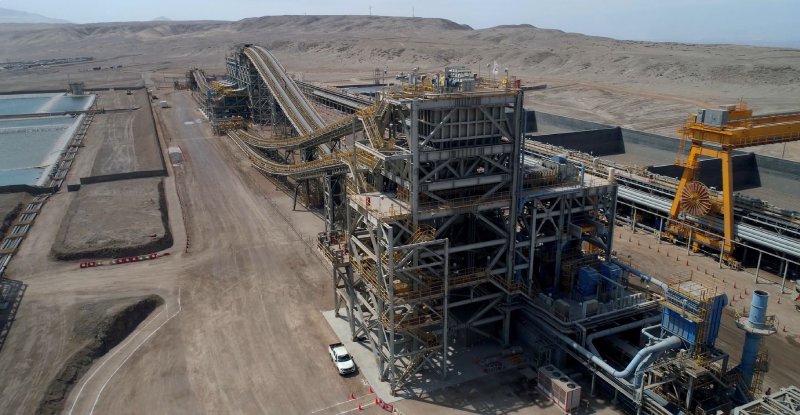
A sophisticated plant designed to achieve the best economic outcomes
To improve project economics, the mine plant at Mina Justa allows for the oxide and sulphide ore deposits to be processed simultaneously, thus targeting the higher-grade sulphide ore early in the project cycle. The design includes two high pressure grinding roller systems, one for each of the oxide and sulphide ore systems.
In terms of crushing, each system is explicit for each orebody and no two crushing systems are alike. At Mina Justa, the combination of the physical characteristics of the ore, combined with the need for vat leaching, required the design of a challenging crushing circuit to feed both the oxide leaching plants and the sulphide concentrator plant. There are eleven crushers in the circuit.
To achieve the best economics, the ore is oxidised using vat leaching which involves loading the ore into large concrete containers, lined with acid resistant material, and flooding the ore with concentrated sulfuric acid to recover the copper in an enriched solution for further processing. The vat leaching facility will be significant: each vat is huge, measuring 46 m x 36 m x 14 m, with 15 vats in the train, measuring 700 m in length.
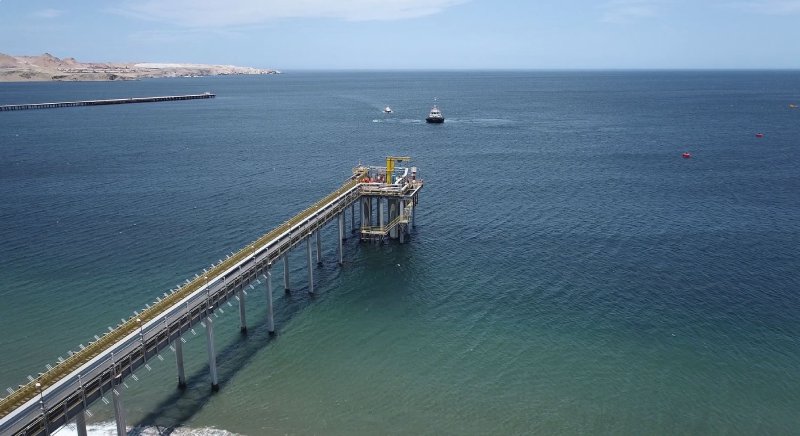
A complete mine-to-port solution with minimal impacts on marine ecosystems
There is a significant amount of external infrastructure required to support the Project, including a marine entrance from Marcona and 40 km of underground pipeline that provides seawater to the site. Ausenco developed the offshore facility within the operating port for the importation of sulfuric acid and pumping of seawater for the process plant.
Mina Justa will consume a shipment of acid every eight to twelve days. The acid will be shipped to Marcona, unloaded into storage tanks and then trucked to the operation. There will be approximately 40 truckloads per day. Our challenge was to design a facility with low impact on local fishing, navigation, and marine life.
The seawater pumped to the plant is desalinated before being used in the process plant and for dust suppression. Seawater desalination and water balance is an area of our expertise proven by multiple desalination systems around the world. Recently, we delivered Carrapateena Copper Mine EPC project in Australia where hypersaline water (five times saltier than seawater) is treated through a Reverse Osmosis plant to produce fresh water with a chemical balance suitable for running the entire plant, especially the peripheral services and non-process infrastructure.
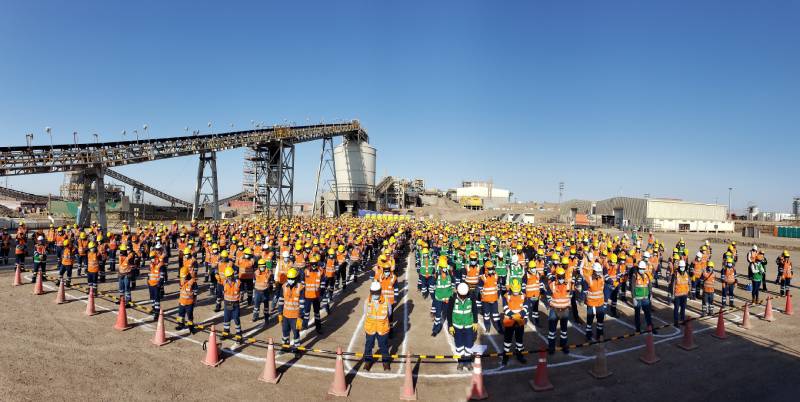
Delivering on schedule despite a pandemic
Thousands of people worked on the Project, most of them Peruvian. Despite the two-month shutdown in Peru in early 2020 due to the pandemic, the team worked towards the committed schedule and progressively started up certain areas of the plant.
In September 2020, Marcobre recognised Ausenco for its efforts to prevent and avoid the spread of COVID-19 at Mina Justa, as demonstrated through actions and meeting all requirements to pass the ‘Audit of Evaluation and Certification of Compliance with the Biosafety Protocol’ by Bureau Veritas.
In February 2021, Marcobre and everyone working on the project surpassed 10 million person hours without a Lost Time Incident (LTI). 6.5 million of these hours correspond to our EPCM work (Ausenco employees and contractors), setting a record for LTI-free hours for the team. This is especially rewarding as this work was carried out not only during a pandemic, but also through challenging commissioning activities.
As of July 2021, the project was fully commissioned. Marcobre obtained operating authorisation and the project entered commercial production.
For more information, please contact Peter Mayall.