Creating a sustainable battery value chain for electromobility
By 2030, more than 30% of all new cars will be electric vehicles, including hybrids. Battery cell manufacturers are investing and building Gigafactory sized production with an increased focus around Europe and North America markets. As one of the leading cathode active materials producers globally, BASF has been establishing a global footprint in Asia, Europe and North America.
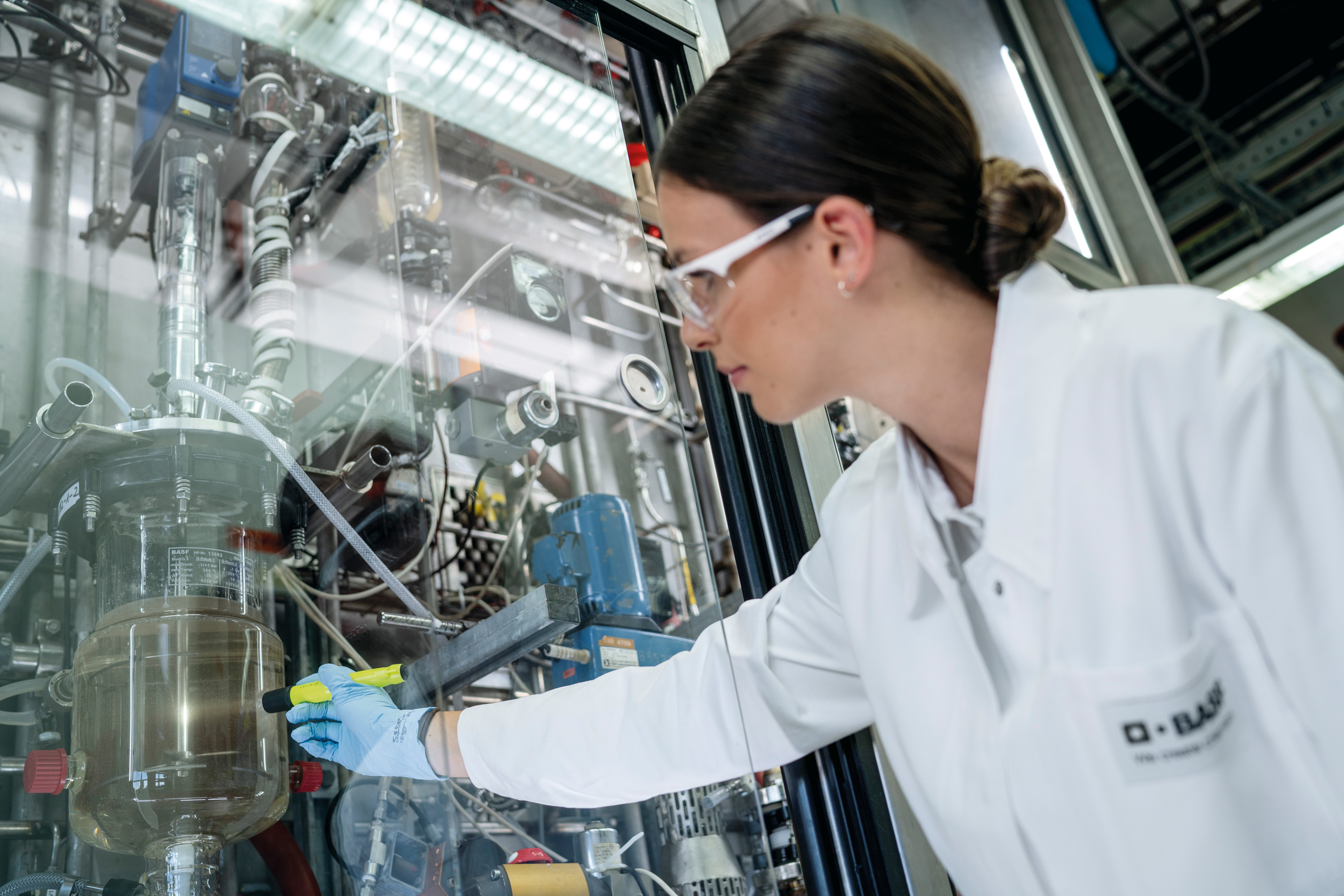
One of the most critical pieces of technology that powers an electric vehicle (EV) is the lithium-ion battery, and the crucial component within the battery that determines the overall performance of EV's is the cathode active materials (CAM).
Sales of EV's (including fully electric and plug-in hybrids) doubled in 2021 to a new record of 6.6 million, with China and Europe as the major contributors to growth.2 With demand increasing for electromobility worldwide, the market for CAM are projected to be worth billions globally, with an annual growth rate of around 21% till 2030.1
The unstoppable growth of EV's also make us think how to give battery materials a new life when an EV reaches its end-of-life. We simply cannot just toss the vehicle to the junkyard but must find ways to recycle the critical materials from lithium-ion batteries. At BASF, we are developing "close-the-loop" solutions to save the materials from these end-of-life batteries and recycle them into raw materials for new batteries to enable a circular economy. The company will build a commercial scale battery recycling black mass plant at its cathode active materials (CAM) production and recycling hub in Schwarzheide, Germany, with start-up planned for early 2024.
BASF is committed to sourcing raw materials in a responsible and sustainable manner. It has been actively partnering with companies around the globe to improve transparency and traceability of critical minerals for batteries to create a sustainable battery value chain.
Built on the company’s 157 years’ experience in the chemistry innovations, BASF Mining Solutions has been supporting the transformation of electromobility by using both chemical and digital solutions that improve the sustainability profile of mineral extraction, which is at the beginning of the battery value chain. It offers sustainable solutions that increase productivity, recovery and flexibility throughout the mining operations including leaching, solvent extraction, flotation, solid/liquid separation, and tailings management, and reduce emission at the same time.
Partnering with IntelliSense.io, BASF also provides artificial intelligence solutions designed to improve process efficiencies, maximize revenues, and assist our customers to strengthen their sustainability and safety efforts for the mining industry,
Sponsored article by BASF, Sustainability Sponsor and Exhibitor at the Lithium, Battery, and Energy Metals Conference 2022.
For more information visit www.basf.com
References:
- BASF Capital Market Story, Feb. 2022.
- Global electric car sales have continued their strong growth in 2022 after breaking records last year - News - IEA